Optimizing Mining Operations with Pitram and Loadscan Integration at CSA Cobar The MAC [...]
Trucking Factors explained
…and how they can be optimized with the MPS Mine Payload Scanner.
Loadscan’s mining technology enables mines to calculate trucking factors with the MPS Mine Payload Scanner. Trucking factors is a collective term used in the mining industry to describe the various elements that are related to the use and deployment of trucks. Ultimately, cost-per-tonne hauled is the key factor that affects bottom-line profitability. It is influenced by numerous sub-factors that can be tracked independently.
That said, the primary factor that influences and determines cost-per-tonne hauled is the actual measured volume of material loaded into a truck bin compared to the truck’s nominal payload capacity, as specified by the manufacturer. Capacity utilisation has a direct relationship to operating costs, with underutilised trucks increasing operating costs and cost-per-tonne hauled.
From our experience, some mines use the nominal payload capacity as a measure of all loads, whilst others might use an estimated average underload factor (e.g. 5%) to measure and account for material being shifted by their trucks. Whilst these are both simple systems to apply they don’t provide an accurate measurement of actual material shifted, delivered to the mill or to the stockpile. In both cases accuracy can be substantially compromised, making reporting and planning challenging.
Let’s consider an example of a mine with five 60T trucks each running 10 loads per shift, 3 shifts per day. Total material shifted at nominal capacity is 9,000T per day (3.285mT per annum). If you apply a conservative average underload factor of 5% to the 60T capacity, you get an average payload of 57T per truck. This would result in 3.121mT actually shifted annually, a significant reduction from nominal (-164,000T), adding up to nearly 2,900 extra trips each year.
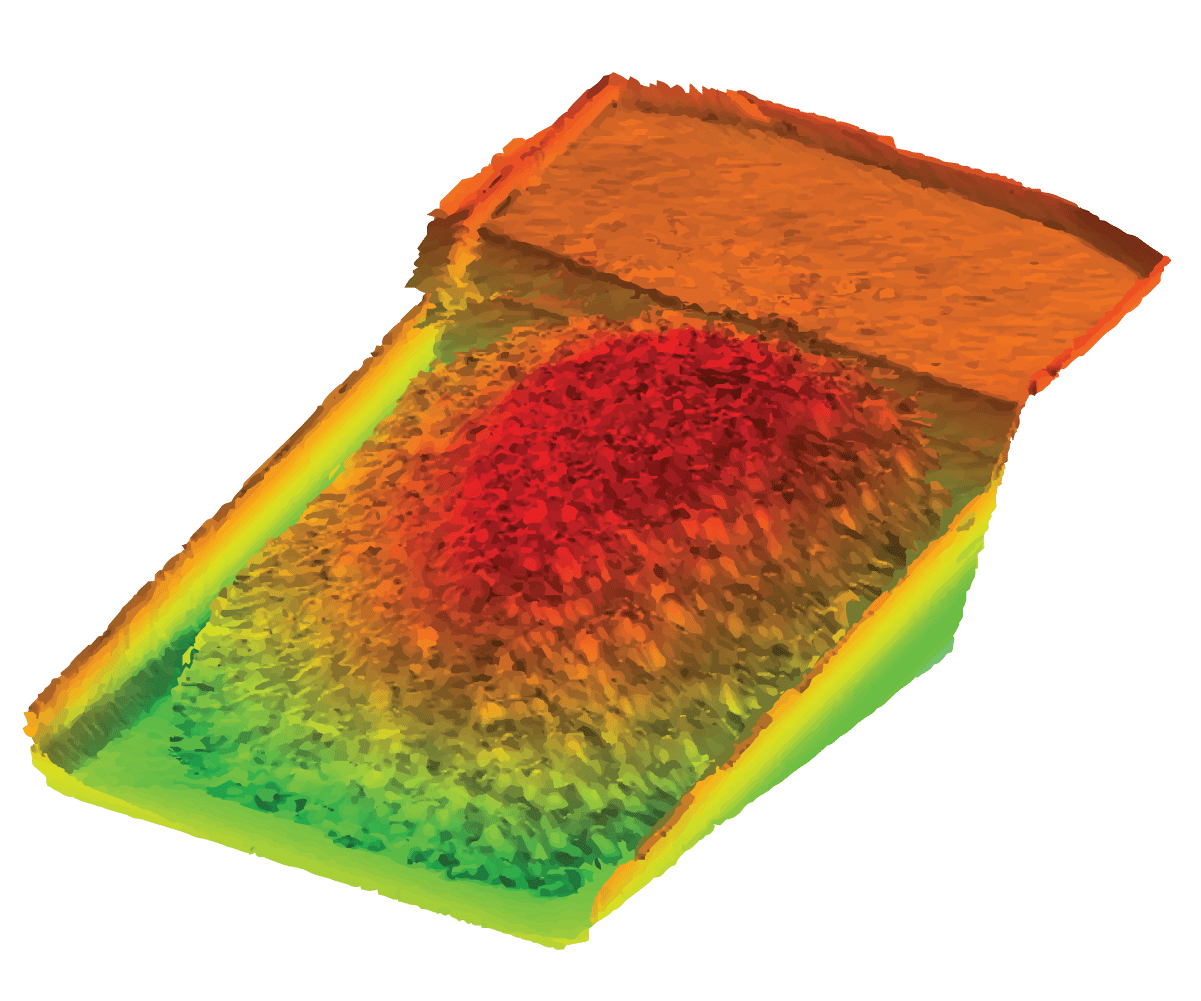
Underloaded
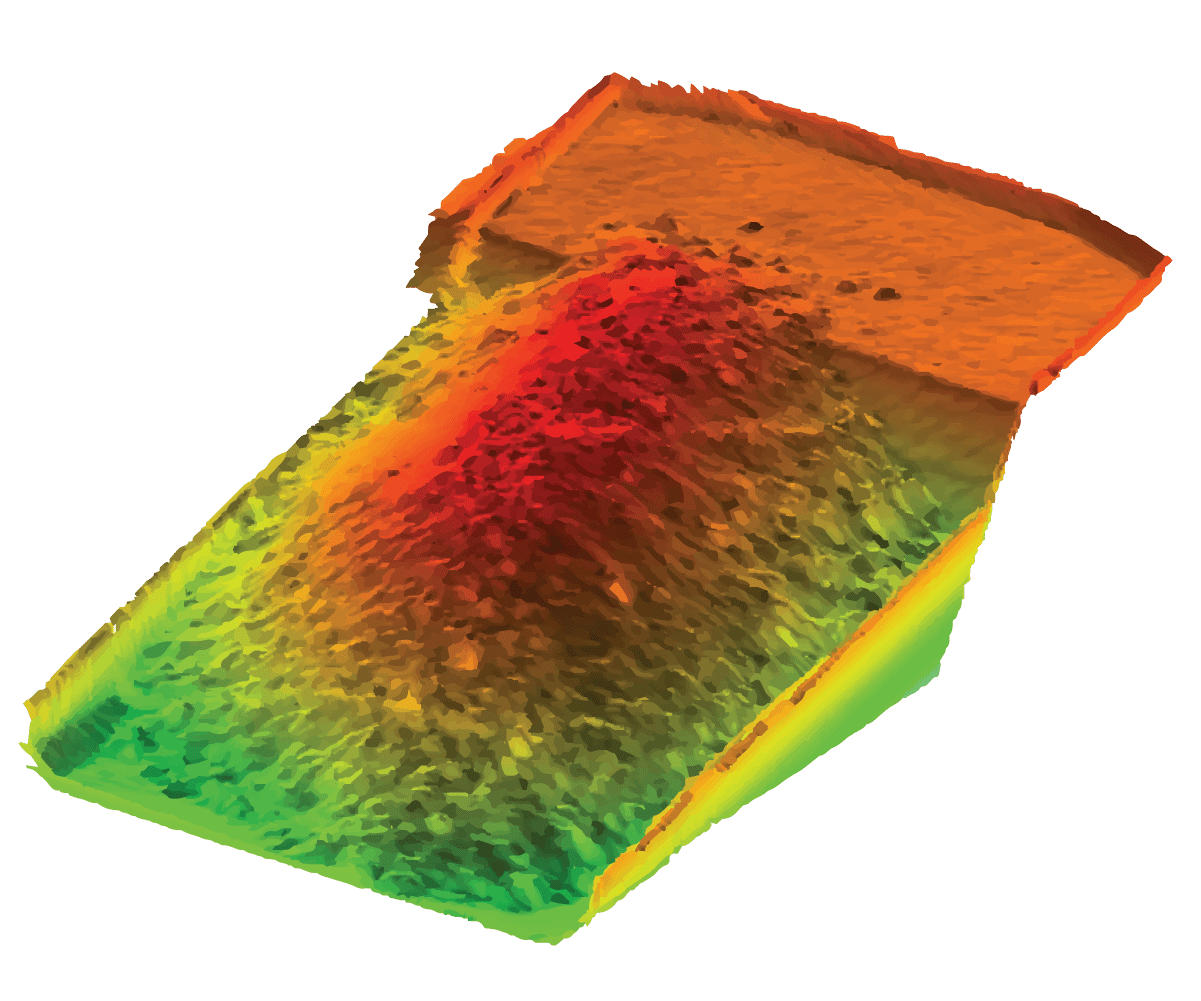
Optimally loaded
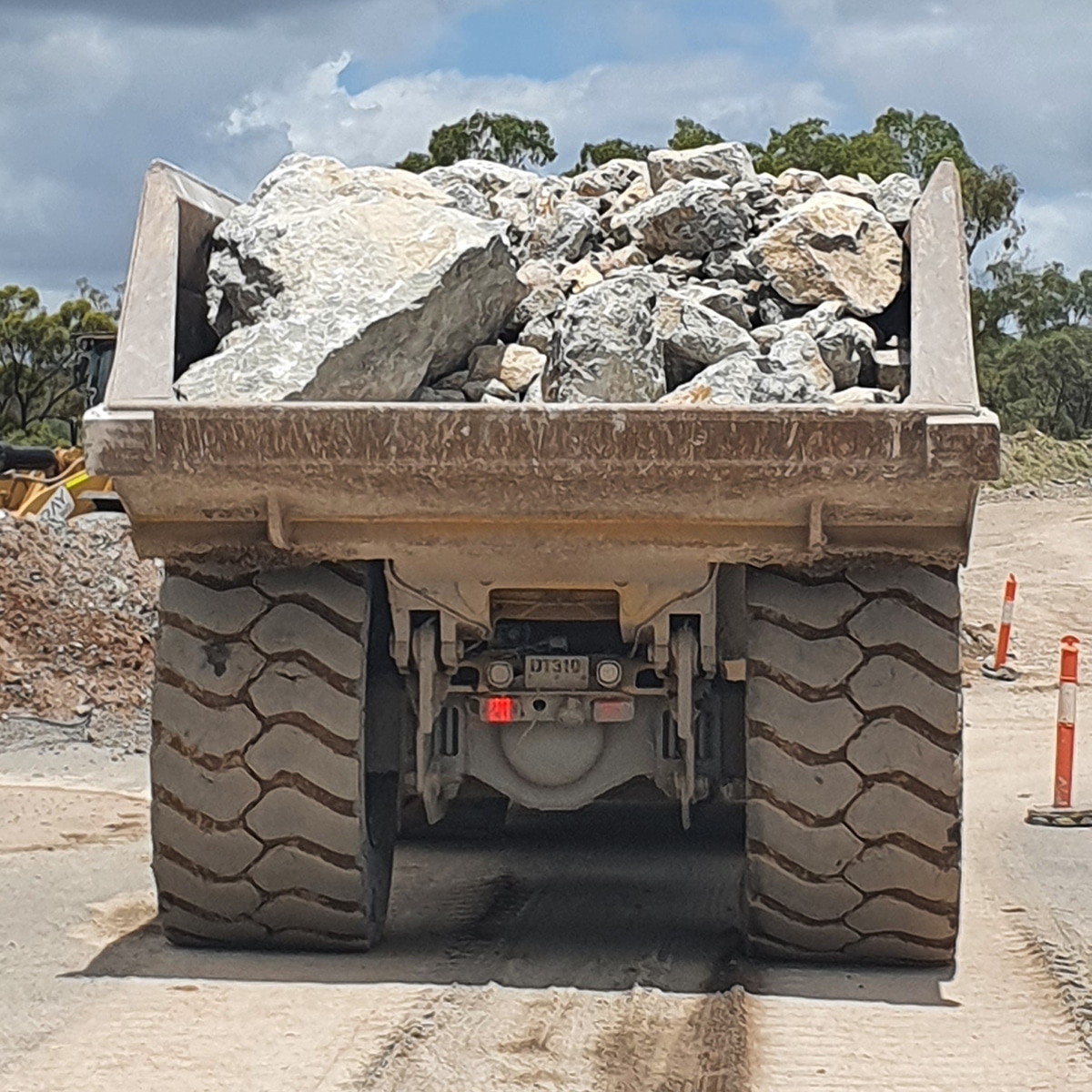
From onsite load audit studies we’ve conducted and measurement results from installed LVS scanners, we typically find that mine trucks are on average underloaded anywhere between 5-15%, and in the worst cases we’ve seen 20-25%. This can have huge production and financial implications to a company mining any value of material, even low-grade overburden.
The previous example is based on tonne weight of material moved (mines typically deal in weight and not volume). You may ask why you would use a scanner measuring cubic volume and not a weighbridge to measure truck loads, and how a volumetric scanner can improve trucking factors.
Some mines might run a single truck with an onboard scale and keep that truck scale calibrated, or they might have a set of scales that are positioned to the side of the haul road, intermittently weighing trucks to check how they’re being loaded. They generally won’t stop every truck on the weigh bridge as it’s too slow and might reduce productivity by as much as 1-2 loads each shift. The other issue with using weigh scales is that inground weighbridges require a lot of routine maintenance (i.e. downtime). Dynamic weighing systems can also be inaccurate.
In this instance, because they are not using a weigh system for every load they will be applying a standard trucking factor to each completed load, which is inaccurate and causes major discrepancies between the haulage department (or contractor) and the mill (or processing plant). For example, the haulage department might say they delivered 400T to the ROM (Run Of Mine) pad. When the processing plant processes the material they might weigh it at 360T, 10% less than what they would have paid to the haulage department or contractor.
By using the Loadscan MPS there are significant benefits and gains to be made which can increase trucking factors, productivity and bottom line results.
Whilst the MPS measures volume it can convert this to tonne weight based on a known bulk density factor. Accurate bulk density factors for each material grade can be established and cross-checked by running a truck over the scale or using the onboard scale to obtain the weight of the material, and then performing a factor calculation against the volume measurement generated by the MPS i.e. Tonne/Volume = bulk density (60T/32m3 = 1.875 bulk density factor). In other words 1m3 weighs 1.875T. So if the material being hauled has a bulk density factor of 1.875, then the 60T truck should be carrying 32m3 of material.
Volume scanning is complementary to measuring weight with scales. By combining weight and volume, measuring material bulk densities and payloads is more accurate.
At a recent mine installation we measured three trucks (60T/32m3 bin capacity) after setting up the MPS system. The measured loads were 28.5m3, 29.8m3 and 24.3m3 respectively, resulting in an average of 27.5m3. Based on these sample measurements we concluded that the trucks were being underloaded by 14% on average.
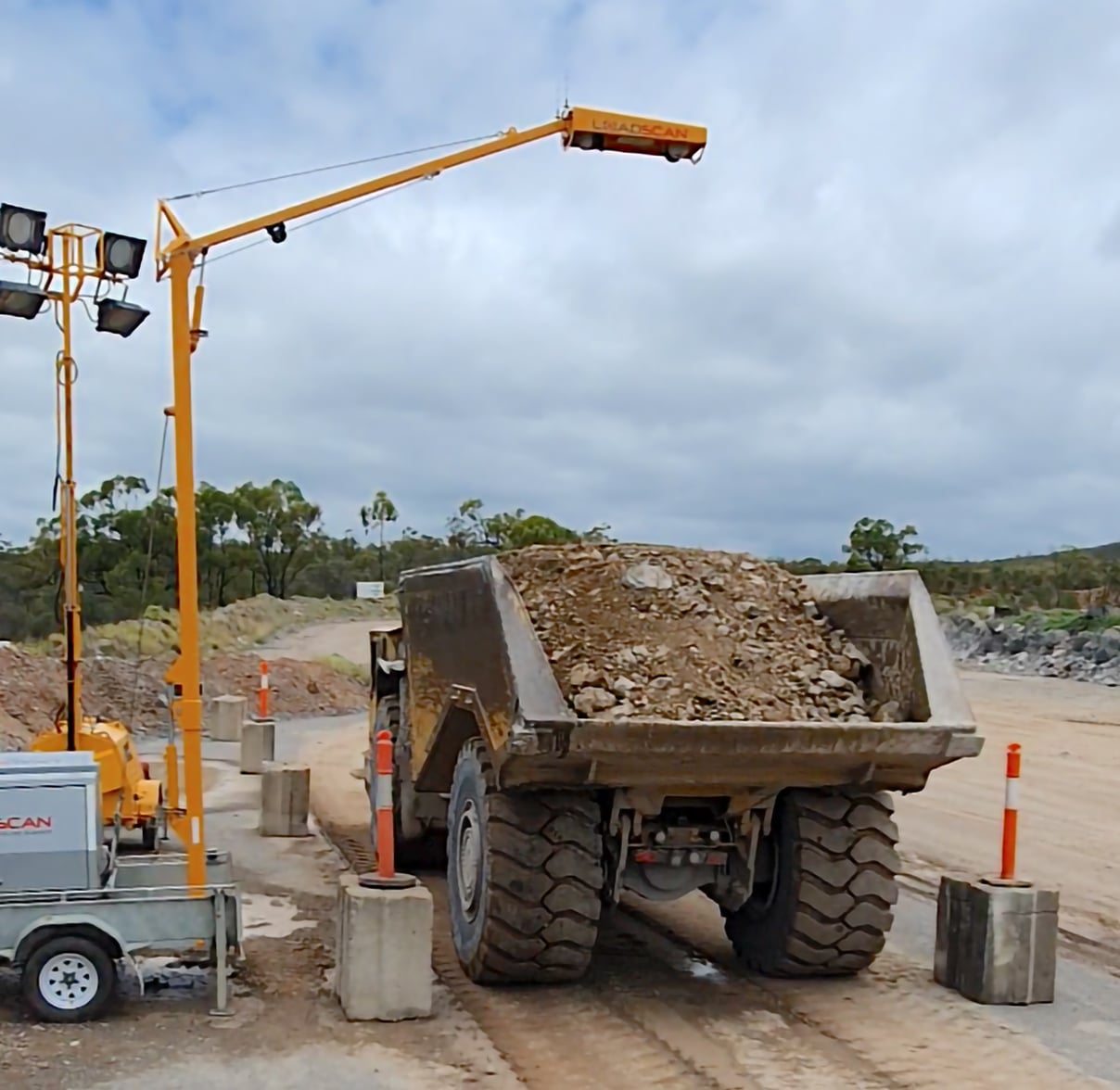
The Loadscan MPS is an automated drive-through system with the measurement result displayed on an LED message board in real-time. Drivers immediately see their load status and can feed back to the loader operator if the load was underloaded or overloaded, preventing further sub-optimal loads (overloading can be dangerous and increases vehicle wear and tear).
A major advantage of the MPS system is that haulage managers can see the results in real time. In mines the MPS system is typically connected to the company network and the results are able to be viewed in their mine management software, or they can use our proprietary MyScanner reporting software. If any loading discrepancies are identified by haulage managers they can take immediate corrective action.
Managers can also view 3D images of every load and save an image file in order to share with loader operators in pre-shift start meetings, enabling ongoing improvement in the loading of trucks. Loader operators become more conscious of their loading practices, knowing they are being watched and checked against an independent, irrefutable system that can’t be manipulated to give inflated measurements, as can be the case with loader/excavator scales.
The direct outcome of implementing a MPS volume scanner is a measurable improvement in trucking factors (and ultimately in profitability). If you would like to benefit from improved trucking factors, please contact us via our enquiry form.