Optimizing Mining Operations with Pitram and Loadscan Integration at CSA Cobar The MAC [...]
Optimizing Mining Operations with Pitram and Loadscan Integration at CSA Cobar
The MAC Copper CSA Mine, located at Cobar, regional New South Wales, is one of Australia’s highest-grade copper mines and among its longest-operating, with a history stretching back nearly 150 years. At 1.9 kilometres (1.2 miles) deep, it is the second-deepest copper mine in Australia. Metals Acquisition Corp (MAC) acquired the CSA mine from Glencore PLC in June 2023. The annual production is approximately 40,000 tonnes of copper each year.
Accurate data is the cornerstone of optimizing mining operations and driving efficiency. At CSA Mine, the Business Improvement (BI) team is dedicated to leveraging advanced tools to improve material tracking and decision-making processes. Recognizing the critical role of informed, data-driven decisions in today’s mining landscape, the mine is embracing cutting-edge technologies to position itself as a leader in innovation and operational excellence.
A key example of this innovation is the integration of Micromine Pitram (a mine control & fleet management system) with Loadscan (a fast and accurate payload measurement system) at CSA Mine. This collaboration is transforming material tracking and management, delivering substantial improvements in accuracy and operational efficiency.
By moving beyond traditional truck factors and manual estimates, the integration provides real-time, precise data for every truck’s load. Leveraging volumetric scanning technology combined with advanced fleet management software, CSA Mine is setting a new benchmark for operational transparency and optimization.
Micromine and Loadscan are proud to partner with the BI team in achieving their goals and ensuring the success of this initiative.
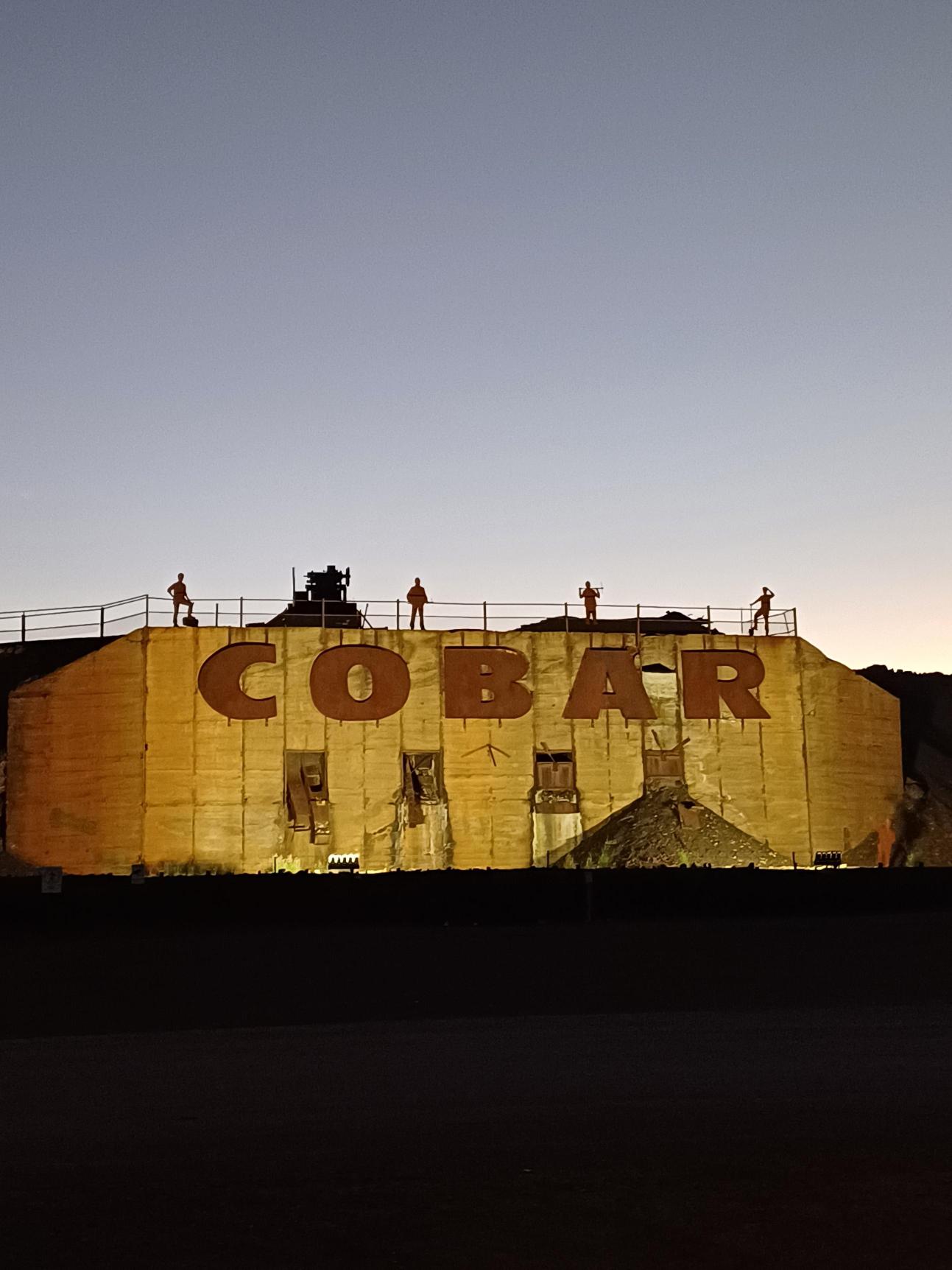
Business Challenge – The traditional approach
Before this integration, like many mining operations, CSA Cobar relied on truck factors —approximate calculations based on truck size and load characteristics — to estimate the amount of material being transported from the underground mine to the surface. While this method was a necessary approximation, it lacked the precision needed to make the best operational decisions.
This reliance on estimates posed several challenges:
Inaccuracy in Load Data: Estimates based on truck factors could lead to discrepancies in tonnage reporting, impacting inventory management, scheduling, and financial reporting.
Limited Visibility: Mine control teams could not directly view the material being hauled, making it harder to verify that the correct material was being transported or to address operational inefficiencies in real-time.
Operational Inefficiencies: Without precise data, optimizing key performance metrics like Truck Kilometres per Tonne (TKM) was difficult, leading to suboptimal fleet performance, higher fuel consumption, and increased wear and tear on equipment.
Objectives
The new Pitram and Loadscan integration at CSA Cobar addresses these issues by providing a seamless flow of real-time, accurate data about truck loads from underground to surface. This would enable better decision-making and operational control through enhanced visibility and utilization metrics.
Technology Solution – Pitram and Loadscan Integration
A new connector has been implemented to collect data from the Loadscan volumetric scanning system. The process begins with Loadscan’s Mine Payload Scanner (MPS), a volumetric portal scanner, which is located at the 9040 level underground. As trucks pass through the scanner, the system uses advanced 3D laser scanning technology to capture the precise volume of material in each truck’s load.
Instead of relying on estimates, the system now delivers accurate, volumetric data directly into Pitram’s Fleet Management System via an API connection. Pitram then uses this data to track the performance of each truck, calculate tonnage more accurately, and generate key performance indicators (KPIs) like TKM.
In addition, Loadscan’s MPS can also be used to monitor haulback of material back into the mine portal Haulback can seriously impact the efficiency of the ore hauling process and the accuracy of daily shift tallies. However, by highlighting the problem, it allows the truck bin to be scraped clean prior to beginning its next trip. This considerably reduces the negative impact haulback has on the efficiency of the transportation cycle.
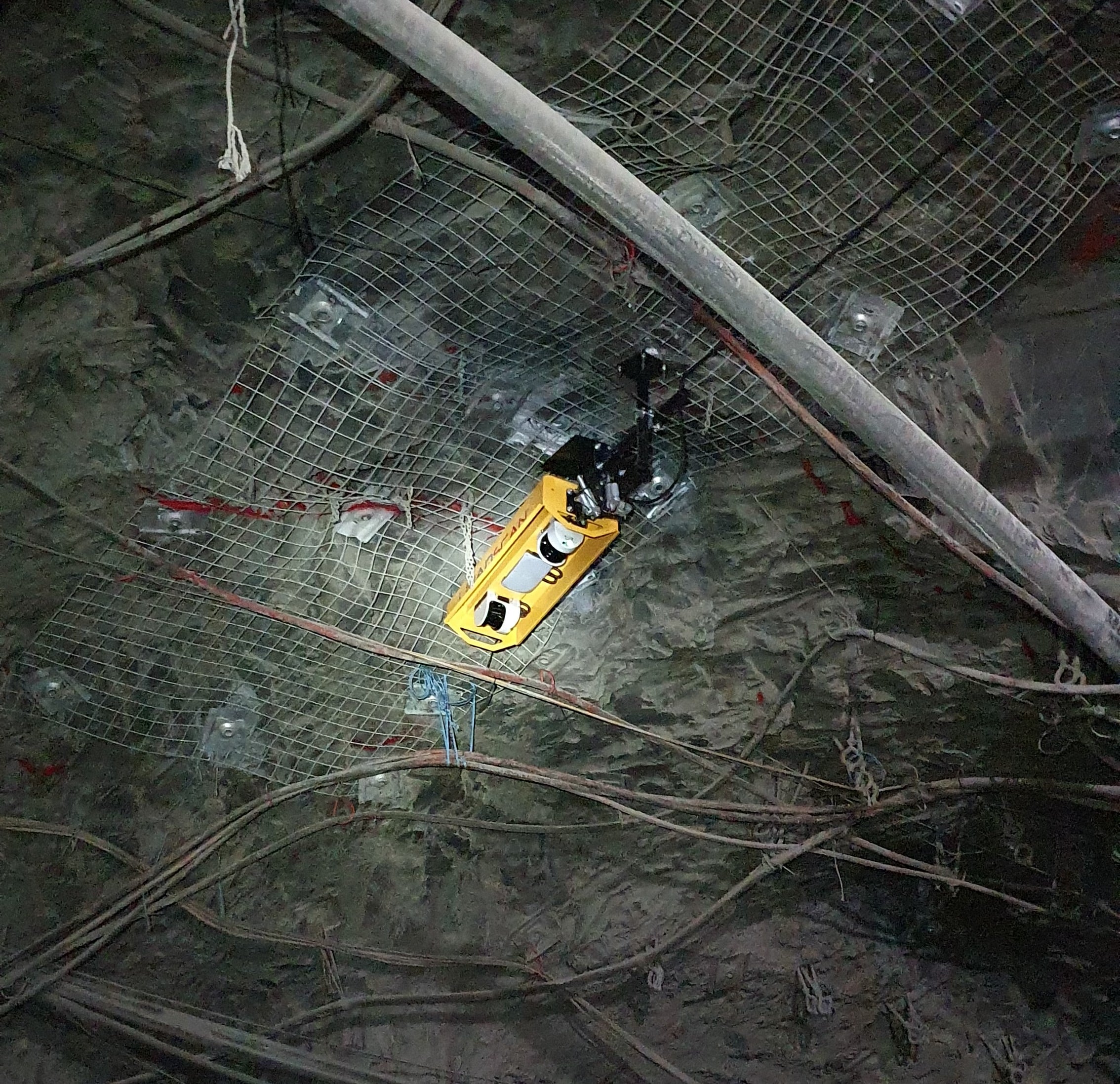
Advanced Features: Real-Time Dashboards and Visual Monitoring
At CSA Cobar, the integration goes even further by incorporating a vision camera into the Loadscan scanner. This camera allows mine control operators to view the material in each truck in real-time, adding a crucial layer of visibility and verification.
In the mine control room, a set of custom dashboards will be used to monitor various operational parameters, including:
Loadscan Analytics: Real-time volumetric data from Loadscan will be displayed on the dashboard, showing the exact amount of material being transported in each truck. This eliminates the need for estimates, providing mine control teams with the most accurate load data available.
Target Tracking: Operators will be able to monitor performance targets in real-time, such as desired truck efficiency, load weight, or TKM goals. This allows them to track progress against predefined targets and take immediate action if performance falls below expectations.
Live Camera Feed: The integration includes a live camera feed from the Loadscan portal scanner, enabling operators to visually inspect the material in the truck. This provides an extra level of confidence that the correct material is being moved and helps identify any potential issues with material quality or discrepancies before they become problems.
Performance Insights: The Pitram dashboard will show real-time data on truck performance, including load efficiency, fleet utilization, and truck trip times. This helps identify bottlenecks or inefficiencies in the system, ensuring that the operation runs smoothly and cost-effectively.
Benefits to CSA: More Accurate Data, Greater Efficiency
The integration of Pitram and Loadscan offers several immediate and long-term benefits for CSA Cobar. The Business Improvement team at CSA played a key role in implementing these insights, ensuring the integration aligns with operational priorities and delivers measurable improvements.
Accurate Load Data: With volumetric scanning technology, the need for truck factors is eliminated, allowing for real-time, accurate measurement of the material being transported. This leads to more accurate reporting of tonnage and ensures that the correct amount of material is shipped to the surface.
Improved Operational Efficiency: By eliminating guesswork and relying on accurate data, CSA Cobar can optimize fleet performance. With insights into load volume and truck efficiency, operators can ensure that trucks are running at optimal capacity and that resources are being used efficiently. This drives improvements in TKM, reducing costs associated with fuel consumption, equipment wear, and maintenance.
Enhanced Visibility and Control: The vision camera integrated into the Loadscan scanner provides real-time visual feedback on the material being transported. This enhances the ability of mine control to ensure the right material is being hauled and to make quick adjustments when needed. Operators have complete visibility into the operation, improving decision-making and reducing the risk of errors.
Real-Time Data for Better Decision-Making: Pitram’s Fleet Management System delivers instant access to volumetric data and performance metrics, enabling CSA Cobar’s mine control team to act quickly and confidently. From optimizing fleet schedules to adjusting truck loads or pinpointing underperforming vehicles, the system ensures a clear and comprehensive view of operations.
Data-Driven Target Monitoring: The ability to set and track performance targets directly from the dashboard gives operators clear, actionable goals. By monitoring these targets, they can identify inefficiencies and improve overall fleet performance in a way that was impossible with traditional methods.
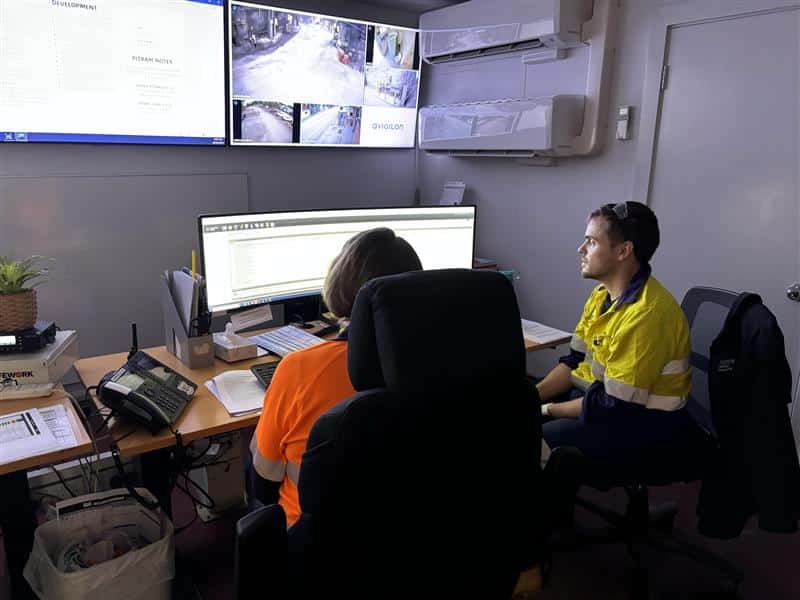
The Bottom Line: Unlocking Efficiency with Precise Data
The Pitram and Loadscan integration at CSA Cobar Mine marks a significant step toward precise, data-driven mining operations. Driven by the Business Improvement team, this solution enhances operational efficiency through real-time volumetric scanning, live material monitoring, and advanced fleet management analytics. By improving load accuracy, fleet performance tracking, and visibility, CSA Cobar reduces costs and boosts efficiency, setting a new standard in mining operations.
The MAC Copper CSA Mine, located at Cobar, regional New South Wales, is one of Australia’s highest-grade copper mines and among its longest-operating, with a history stretching back nearly 150 years. At 1.9 kilometres (1.2 miles) deep, it is the second-deepest copper mine in Australia. Metals Acquisition Corp (MAC) acquired the CSA mine from Glencore PLC in June 2023. The annual production is approximately 40,000 tonnes of copper each year.
Accurate data is the cornerstone of optimizing mining operations and driving efficiency. At CSA Mine, the Business Improvement (BI) team is dedicated to leveraging advanced tools to improve material tracking and decision-making processes. Recognizing the critical role of informed, data-driven decisions in today’s mining landscape, the mine is embracing cutting-edge technologies to position itself as a leader in innovation and operational excellence.
A key example of this innovation is the integration of Micromine Pitram (a mine control & fleet management system) with Loadscan (a fast and accurate payload measurement system) at CSA Mine. This collaboration is transforming material tracking and management, delivering substantial improvements in accuracy and operational efficiency.
By moving beyond traditional truck factors and manual estimates, the integration provides real-time, precise data for every truck’s load. Leveraging volumetric scanning technology combined with advanced fleet management software, CSA Mine is setting a new benchmark for operational transparency and optimization.
Micromine and Loadscan are proud to partner with the BI team in achieving their goals and ensuring the success of this initiative.
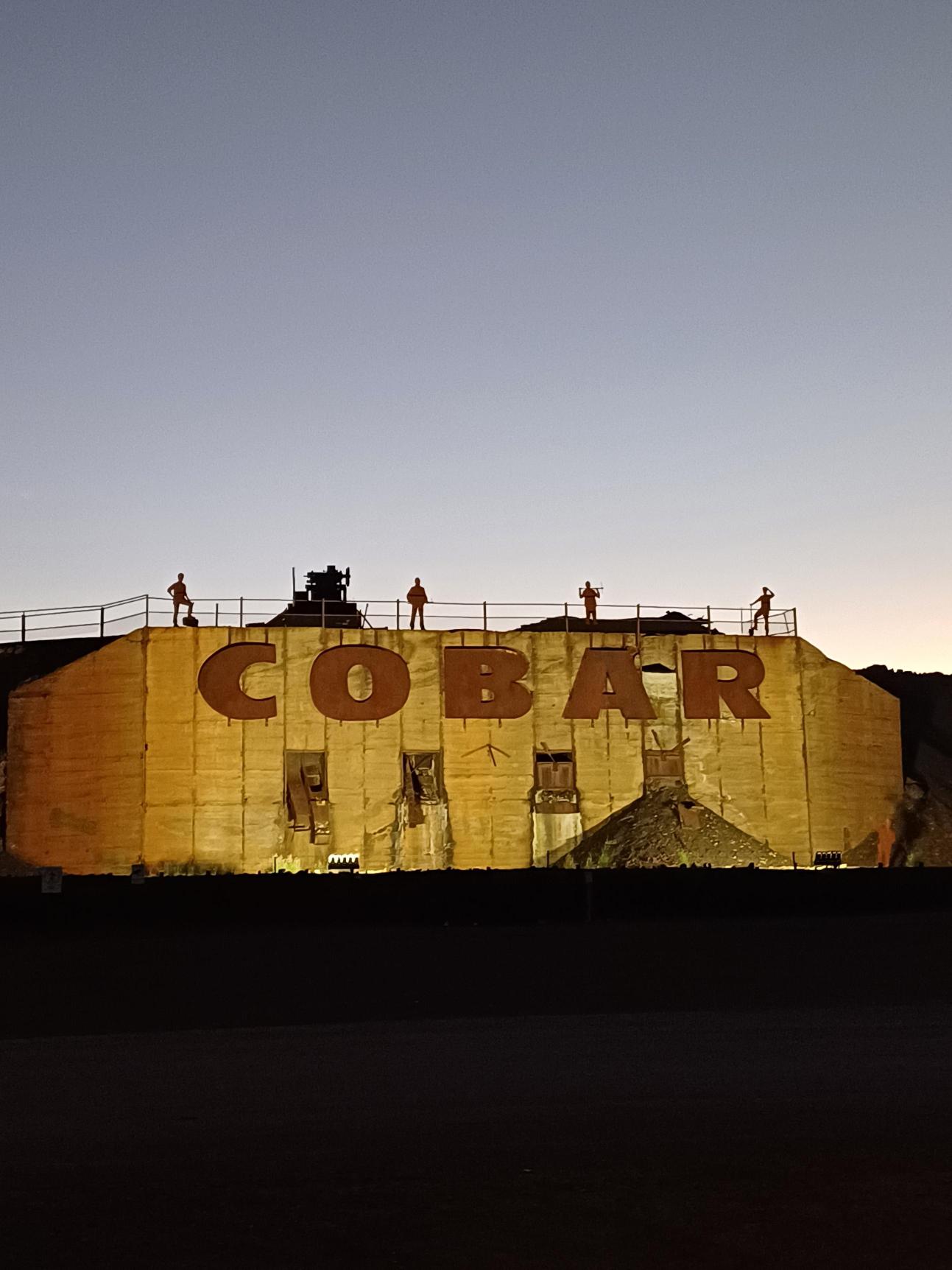
Business Challenge – The traditional approach
Before this integration, like many mining operations, CSA Cobar relied on truck factors —approximate calculations based on truck size and load characteristics — to estimate the amount of material being transported from the underground mine to the surface. While this method was a necessary approximation, it lacked the precision needed to make the best operational decisions.
This reliance on estimates posed several challenges:
Inaccuracy in Load Data: Estimates based on truck factors could lead to discrepancies in tonnage reporting, impacting inventory management, scheduling, and financial reporting.
Limited Visibility: Mine control teams could not directly view the material being hauled, making it harder to verify that the correct material was being transported or to address operational inefficiencies in real-time.
Operational Inefficiencies: Without precise data, optimizing key performance metrics like Truck Kilometres per Tonne (TKM) was difficult, leading to suboptimal fleet performance, higher fuel consumption, and increased wear and tear on equipment.
Objectives
The new Pitram and Loadscan integration at CSA Cobar addresses these issues by providing a seamless flow of real-time, accurate data about truck loads from underground to surface. This would enable better decision-making and operational control through enhanced visibility and utilization metrics.
Technology Solution – Pitram and Loadscan Integration
A new connector has been implemented to collect data from the Loadscan volumetric scanning system. The process begins with Loadscan’s Mine Payload Scanner (MPS), a volumetric portal scanner, which is located at the 9040 level underground. As trucks pass through the scanner, the system uses advanced 3D laser scanning technology to capture the precise volume of material in each truck’s load.
Instead of relying on estimates, the system now delivers accurate, volumetric data directly into Pitram’s Fleet Management System via an API connection. Pitram then uses this data to track the performance of each truck, calculate tonnage more accurately, and generate key performance indicators (KPIs) like TKM.
In addition, Loadscan’s MPS can also be used to monitor haulback of material back into the mine portal Haulback can seriously impact the efficiency of the ore hauling process and the accuracy of daily shift tallies. However, by highlighting the problem, it allows the truck bin to be scraped clean prior to beginning its next trip. This considerably reduces the negative impact haulback has on the efficiency of the transportation cycle.
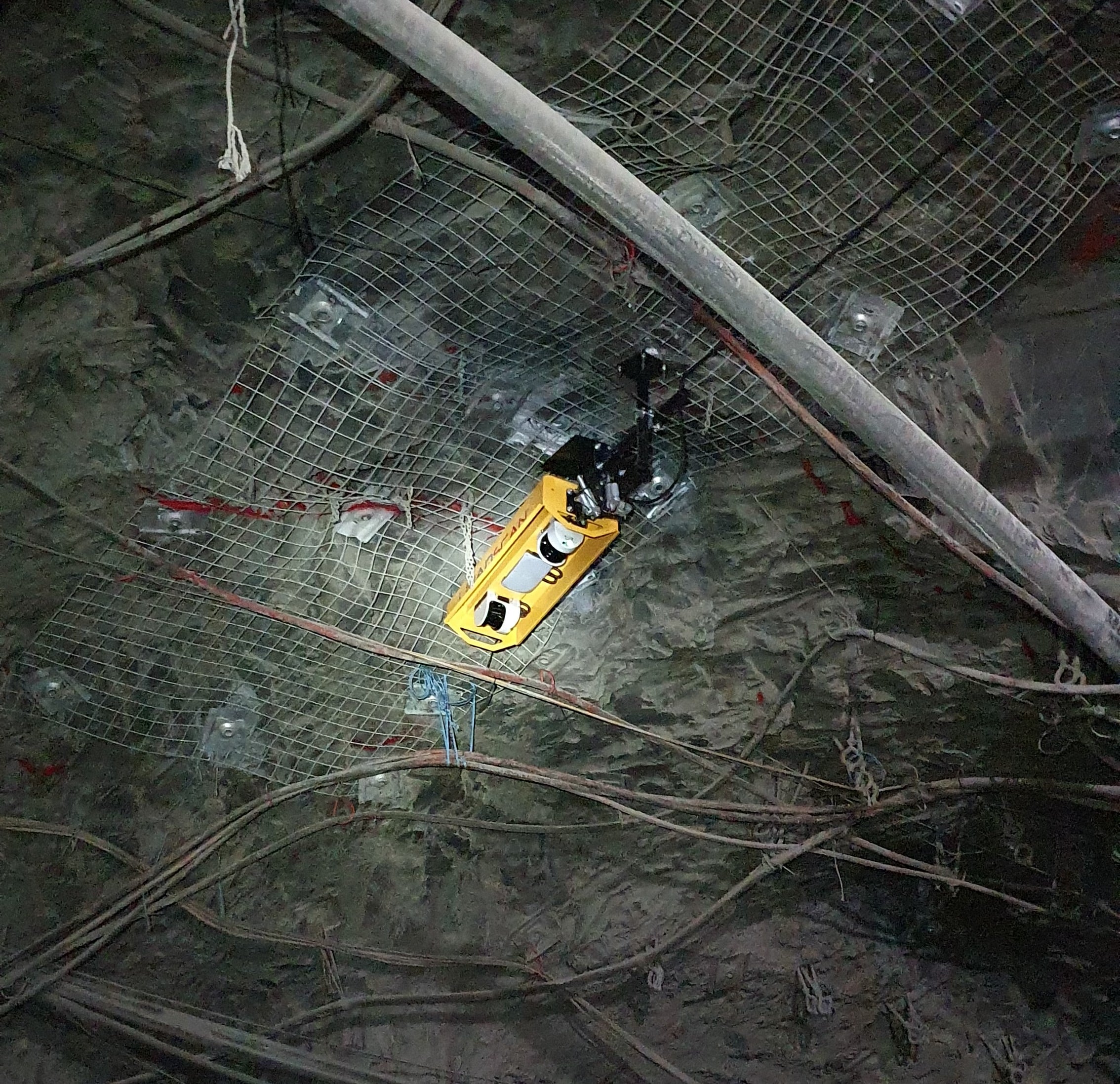
Advanced Features: Real-Time Dashboards and Visual Monitoring
At CSA Cobar, the integration goes even further by incorporating a vision camera into the Loadscan scanner. This camera allows mine control operators to view the material in each truck in real-time, adding a crucial layer of visibility and verification.
In the mine control room, a set of custom dashboards will be used to monitor various operational parameters, including:
Loadscan Analytics: Real-time volumetric data from Loadscan will be displayed on the dashboard, showing the exact amount of material being transported in each truck. This eliminates the need for estimates, providing mine control teams with the most accurate load data available.
Target Tracking: Operators will be able to monitor performance targets in real-time, such as desired truck efficiency, load weight, or TKM goals. This allows them to track progress against predefined targets and take immediate action if performance falls below expectations.
Live Camera Feed: The integration includes a live camera feed from the Loadscan portal scanner, enabling operators to visually inspect the material in the truck. This provides an extra level of confidence that the correct material is being moved and helps identify any potential issues with material quality or discrepancies before they become problems.
Performance Insights: The Pitram dashboard will show real-time data on truck performance, including load efficiency, fleet utilization, and truck trip times. This helps identify bottlenecks or inefficiencies in the system, ensuring that the operation runs smoothly and cost-effectively.
Benefits to CSA: More Accurate Data, Greater Efficiency
The integration of Pitram and Loadscan offers several immediate and long-term benefits for CSA Cobar. The Business Improvement team at CSA played a key role in implementing these insights, ensuring the integration aligns with operational priorities and delivers measurable improvements.
Accurate Load Data: With volumetric scanning technology, the need for truck factors is eliminated, allowing for real-time, accurate measurement of the material being transported. This leads to more accurate reporting of tonnage and ensures that the correct amount of material is shipped to the surface.
Improved Operational Efficiency: By eliminating guesswork and relying on accurate data, CSA Cobar can optimize fleet performance. With insights into load volume and truck efficiency, operators can ensure that trucks are running at optimal capacity and that resources are being used efficiently. This drives improvements in TKM, reducing costs associated with fuel consumption, equipment wear, and maintenance.
Enhanced Visibility and Control: The vision camera integrated into the Loadscan scanner provides real-time visual feedback on the material being transported. This enhances the ability of mine control to ensure the right material is being hauled and to make quick adjustments when needed. Operators have complete visibility into the operation, improving decision-making and reducing the risk of errors.
Real-Time Data for Better Decision-Making: Pitram’s Fleet Management System delivers instant access to volumetric data and performance metrics, enabling CSA Cobar’s mine control team to act quickly and confidently. From optimizing fleet schedules to adjusting truck loads or pinpointing underperforming vehicles, the system ensures a clear and comprehensive view of operations.
Data-Driven Target Monitoring: The ability to set and track performance targets directly from the dashboard gives operators clear, actionable goals. By monitoring these targets, they can identify inefficiencies and improve overall fleet performance in a way that was impossible with traditional methods.
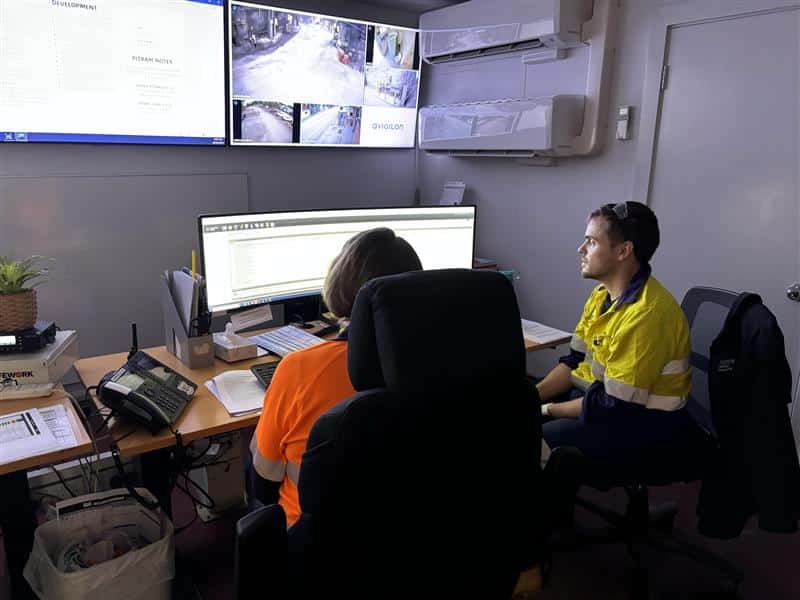
The Bottom Line: Unlocking Efficiency with Precise Data
The Pitram and Loadscan integration at CSA Cobar Mine marks a significant step toward precise, data-driven mining operations. Driven by the Business Improvement team, this solution enhances operational efficiency through real-time volumetric scanning, live material monitoring, and advanced fleet management analytics. By improving load accuracy, fleet performance tracking, and visibility, CSA Cobar reduces costs and boosts efficiency, setting a new standard in mining operations.