Optimizing Mining Operations with Pitram and Loadscan Integration at CSA Cobar The MAC [...]

Loadscan enhances operational efficiency at Pro Bark Industries
Project Details
CATEGORY: | Bark, Mulch & Compost |
LOCATION: | Plaistow, New Hampshire, USA |
WEBSITE: | probark.com |
Pro Bark Industries, located in Plaistow, New Hampshire, is a leading producer of mulch, compost, soil, and other organic products.
The operation is just one of the diverse Mayer group of companies and produces around 200,000 yards of material each year, servicing a wide variety of customers, including large garden centres, landscaping companies, and even homeowners who need bulk products.
Pro Bark operations manager, Rory Holmes, says Loadscan’s Load Volume Scanner (LVS) has streamlined their processes, improved accuracy, and significantly increased efficiency to the way the business operates.
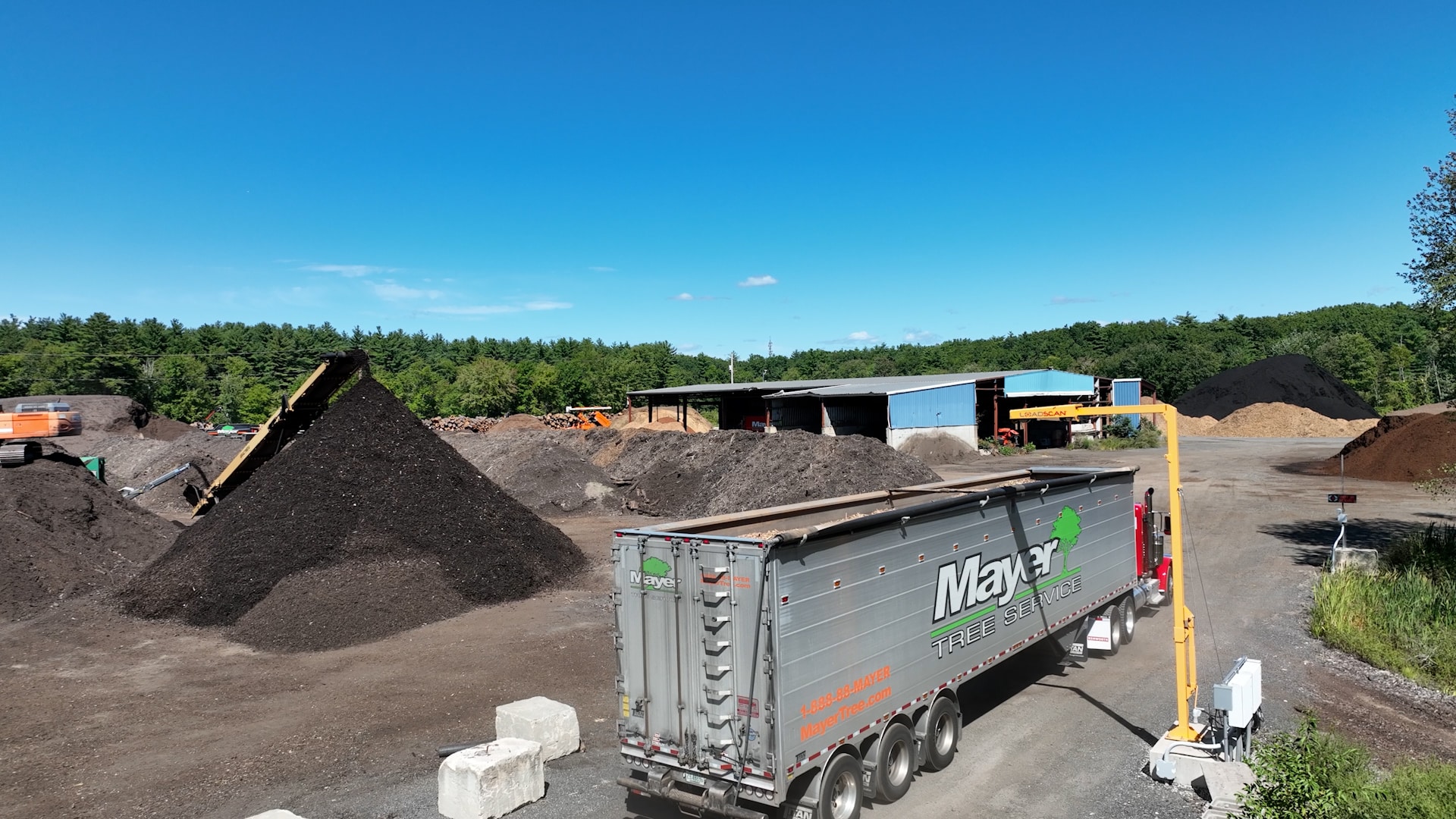
The challenge of accurate measurement
At Pro Bark Industries, accuracy in measuring outbound material is critical. With such a high volume of material leaving the yard annually, precise volume measurements are critical to ensure accuracy.
“We normally don’t scan in, because it’s not as important to for us to count the yardage as it comes in because it gets sorted out into different products,” Rory explains. “For us, it’s really important outbound to know what the yardages are,”
Before implementing Loadscan, Pro Bark relied on a manual process for measuring material volume. Loader operators would estimate the amount of material by counting the number of loader bucket scoops and multiplying by the known yardage of the bucket, typically 12 cubic yards. However, this system was far from perfect.
“You’re kind of guesstimating; the loader operators basically just count buckets. They know the yardage of the machine bucket and then they go from there. But it’s definitely not ideal to do it that way because there’s quite a bit of guesswork that that goes into that way of doing it,” Rory admits.
This process was prone to errors. Depending on how the material was scooped or how consistent the loader operator was, the volume could vary – sometimes significantly.
“A loader bucket is built to a certain amount of cubic yards. We usually run 12-yard buckets but, depending on how you dig into a pile or whatever happens if you shake out too much or you don’t shake out enough, you might you might be at 10 yards or you might be at 15 yards,” Rory explains.
Over time, this led to inconsistencies in volume and, ultimately, could affect both customer satisfaction and inventory management.
Enter Loadscan: A revolution for Pro Bark Industries
In the spring of 2024, Pro Bark decided to address this issue by installing the Loadscan LVS. The system immediately transformed how they handled volume measurement.
“We installed it for this previous mulch season, which would be in the spring for us,” says Rory.
Loadscan’s system uses LIDAR laser technology to scan each truckload as it exits the yard, providing precise volume measurements in real time. For Pro Bark, this meant no more reliance on visual estimates or rough calculations. The system provides an instant, accurate reading of the volume in each load, removing much of the guesswork from the process.
“If we have a bigger customer that’s in here a lot, then we’ll have them scan into the Loadscan and that way, when they’re outbound, they can scan out and then they’ll be in our system as a customer,” Rory explains.
“What’s nice about Loadscan is that it’s so easy to use. It’s user-friendly for the truck drivers, so they just come into the office, put in their information and then they’re on their way.”
This method ensures that Pro Bark can track all outgoing shipments, accurately record the volume of each load, and keep a reliable inventory.
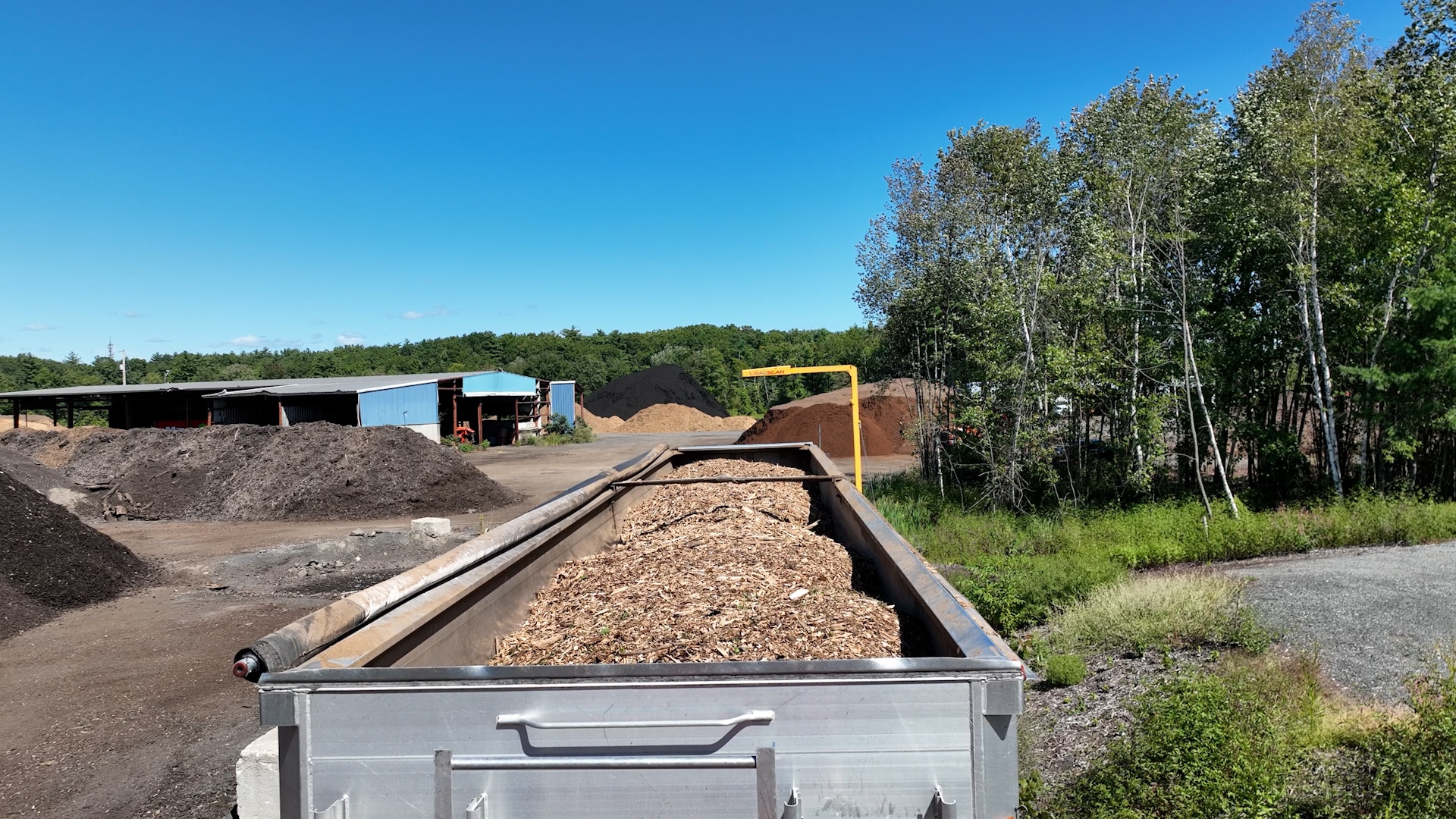
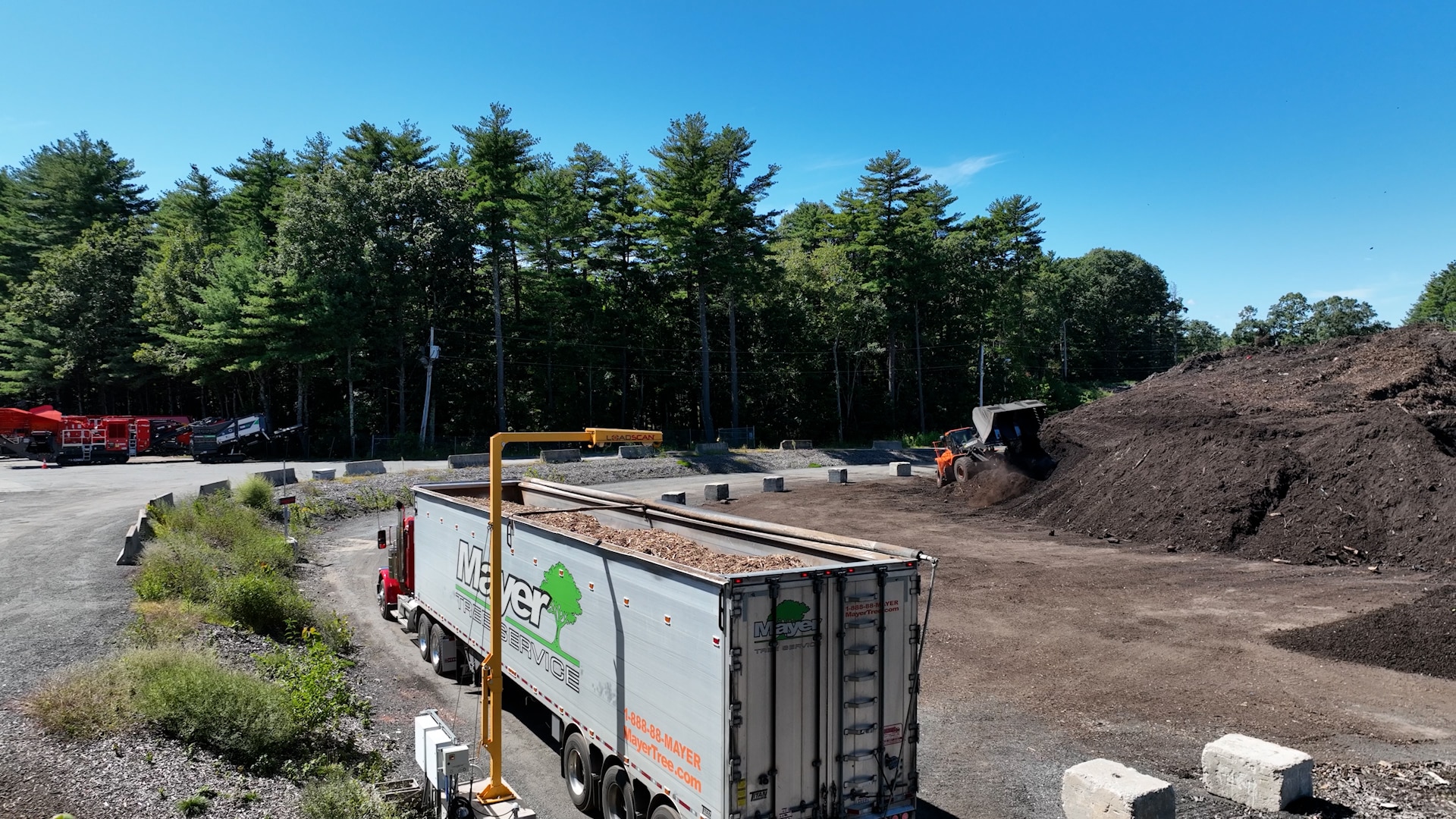
Real-time monitoring for better control
One of the most valuable aspects of Loadscan for Pro Bark has been its real-time monitoring capabilities. Rory now has the ability to keep track of the volume of every load that leaves the yard, from his office.
“It’s nice because being able to have the [MyScanner] cloud app that’s on the computer, I can see every load that comes in, and I can keep up with it as the day progresses,” he explains.
“For example, if I notice that there’s something off with the loader operator loading trucks, and if he’s loading light or heavy, then I can make that phone call and let them know to lighten up or to put more on,” Rory says.
“Also, if you have multiple scanners, you can — on your computer in your office — remotely look into your scanners. So it’s just really convenient to use… and it’s also very accurate.”
This enables him to catch any discrepancies as soon as they occur.
This has helped Pro Bark dial in their volumes for each load and fine-tune the process to ensure that they are consistently hitting their targets.
“I think we’ve really been able to get our average yardage on every load. We’ve really been able to dial that in to get it to where we want it to be, so we’re not giving away too much and we’re not shorting people,” Rory continues.
This precision has been critical to maintaining both Pro Bark’s profitability and satisfaction for its customers.
Preventing overloads and underloads
The LVS system has been instrumental in preventing both overloads and underloads. By providing precise volume data, Loadscan ensures that each truck is filled with the correct amount of material, reducing the risk of delivering too much or too little. Rory notes that accurately measuring loads is particularly important for ensuring fairness in customer transactions:
“You obviously don’t want to short people…or give it away for free either,” he says.
In the past, the manual system meant that occasional inconsistencies could lead to situations where material was lost, or customers weren’t receiving the volume they paid for.
“It adds up at the end of the season, for sure,” Rory points out.
Since the installation of the Loadscan LVS, those discrepancies have been virtually eliminated.
Scalability and industry reputation
Although Pro Bark is still relatively new to using Loadscan, Rory is already seeing the benefits in terms of operational efficiency and customer satisfaction. The system has integrated seamlessly into their day-to-day operations, and they are starting to gather useful data that will inform their long-term planning.
“At the end of the year, we’ll take a hard look at the numbers,” says Rory. “It’s also a great way to make sure that you’re matching the hard numbers to what your projections are.
“If you’re purchasing material, and if that’s getting scanned in, then you want to make sure that you’re not getting shorted and that everything’s adding up, so it’s a good way to failsafe your operations as far as taking in material and then sending it out, so it’s a good way to double check things.
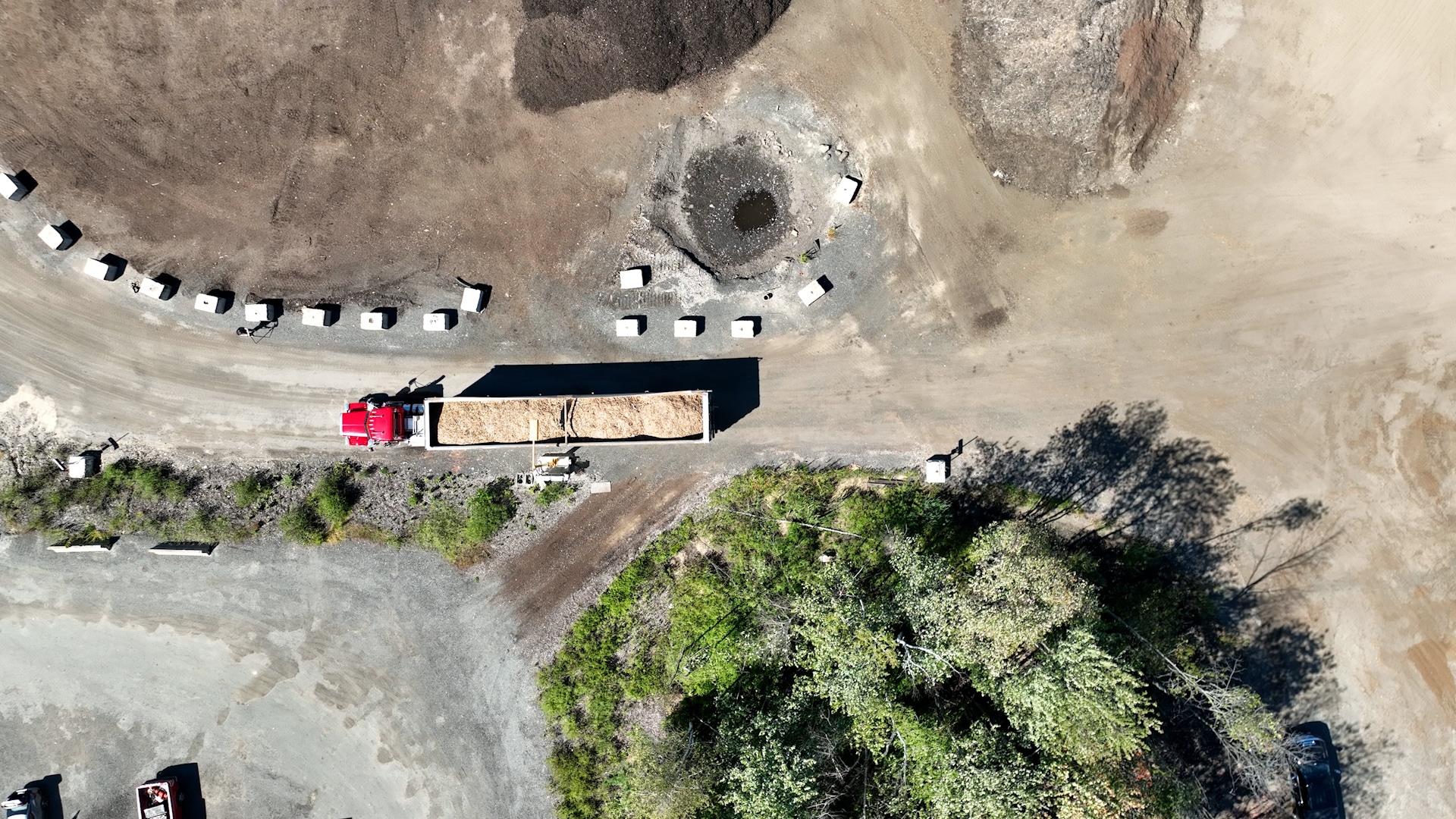
The benefits of Loadscan in handling material variability
Another challenge Pro Bark faces is the variation in material moisture content, which can affect the weight of certain products. Materials like soil can be particularly finicky, as excess moisture can result in varying weights, which is where Loadscan’s LVS provides a clear advantage by measuring volume rather than weight, which eliminates the complications that arise from varying moisture content.
The accuracy of Loadscan’s volume measurements, unaffected by moisture content, has made it an ideal solution for Pro Bark’s operations.
Collaborative industry environment
Pro Bark’s relationships with larger local companies in the bark, mulch and compost industries have also been strengthened by the use of the Loadscan LVS. As Rory explains, many of the other industry players, have a strong history with Loadscan, and rely on the system to track their material volumes.
Loadscan’s reputation in the industry, built on success stories around the reliability and accuracy of the Loadscan system, helped influence Pro Bark’s decision to invest in the technology.
“It was a word-of-mouth situation,” Rory says. “The bigger players have several of them at all their locations and, knowing how much these other companies rely on them and use them and don’t have any issues with it.”
This has created an open, collaborative environment where companies can share knowledge, resources and even customers.
“We tend to play nice with everyone because some companies offer products that we don’t offer,” he explains. “Rather than tell a customer ‘we don’t sell that, sorry I can’t help you’, it’s way more beneficial to make a call and say ‘hey, we have a customer that’s looking for this. We’re just going to resell it to them’, and they’re fine with that.”
A valuable investment for Pro Bark Industries
Rory believes that Loadscan has had a transformative effect on Pro Bark Industries. By providing precise, real-time volume measurements, Loadscan has eliminated the guesswork that previously led to inconsistencies in outbound shipments. The system has not only improved operational efficiency but also provided Pro Bark with the tools to maintain strong relationships with their customers and ensure that each load is accurate.
As Rory sums up, “For something that’s as sophisticated as it is, it’s really user-friendly. There’s no contact. It’s really easy to set up and use as far as the setup goes and how you adjust it.
“It’s just been a big help, for sure.”