Optimizing Mining Operations with Pitram and Loadscan Integration at CSA Cobar The MAC [...]
A celebratory 2019 for Loadscan
The team at Loadscan is celebrating a successful year with many happy customers around the world.
Catering for the mining, bark and mulch, quarries and civil industries, Loadscan is thrilled with the responses they’ve been getting, not only from the quality and innovative solution they provide but from their reliable customer service.
After recently moving to larger premises in Hamilton, New Zealand and opening offices in NSW Australia to meet production demands of their load volume scanner (LVS) and conveyor volume scanner (CVS), Loadscan is set for an exciting 2020.
Loadscan prides itself on building long term relationships with customers after buying their scanner. With 50% of Loadscan’s clients being repeat customers it gives the company global credibility.
Loadscan’s 24/7 support network teams’ main goal is customer success – Loadscan know that time is money and in the rare occasion that there’s complications the team endeavour to get your scanner back on track quickly and efficiently.
Here’s what some of our happy customers of 2019 had to say…
Loadscan’s customer service team has always been available and helpful with keeping our system up and running as well as helping us make personal preference changes to the system.
Kristen Carrier McRae of P.R Russell – Bark and Mulch, USA.
The Loadscan makes everyone aware of the loading capacity and in same time includes awareness of the excavator operator, truck driver and receiving end of loading capacity. Coops, as a Principal Contractor is closely monitor this and if any overloading happens it is easily identified and brought to everyone’s attention. As always, safety comes first. With the Loadscan this is definitely easier to control. Need to mention that Drew is very knowledgeable and supportive as technical assistant on any minor issue or question that we have.
Milos Krivokapic of Coops – Civil construction, Australia.
Loadscan has been helpful to improve operational performance by managing haul-back to reveal our true shift tally. We can now accurately calculate net volumes delivered for processing. Time is also saved by minimizing paperwork, there’s no manual data entry, driver records or after-shift record sorting.
Pavan Kaushik of Hindustan Zinc – Mining, India.
The scanner was measuring significant amounts of carry-back by the contractor. Especially this season where the material was sticky and wet compared to previous years. This was often up to 5mᶾ per load, which on some trucks is 20-25% carry back – obviously a huge saving for us.
Daniel Le Roux of Rodney Aggregates – Quarry, New Zealand.
Loadscan’s new premises is based at 27 Earthmover Cresent, Hamilton, for more information on Loadscan’s products visit www.loadscan.com
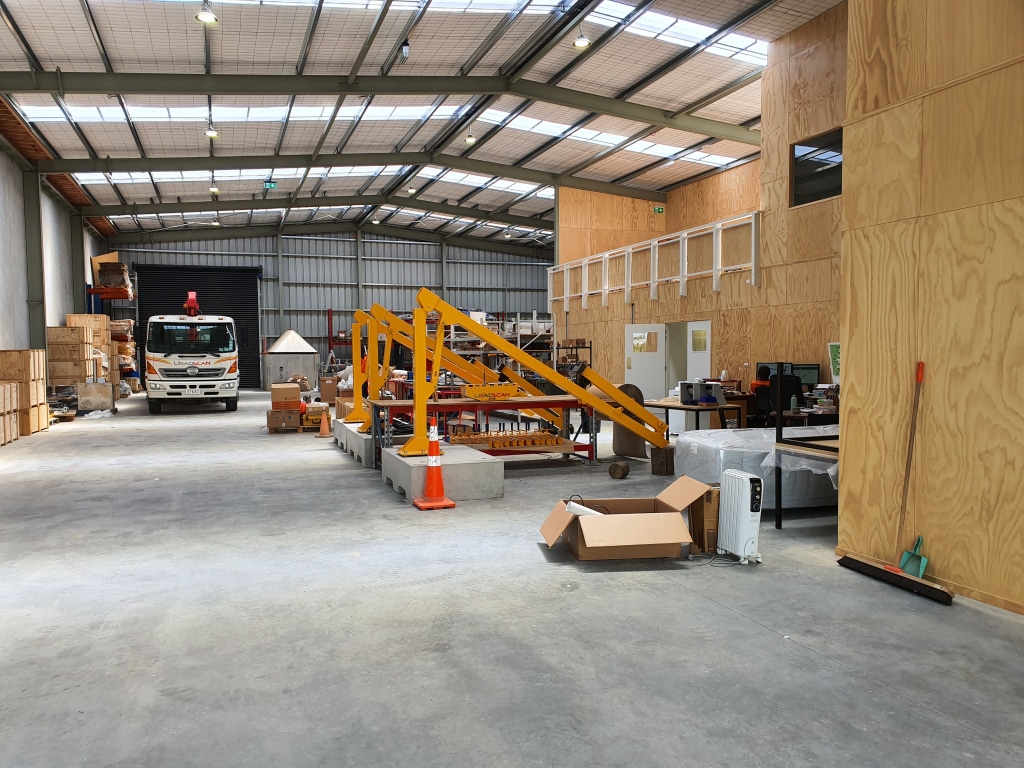
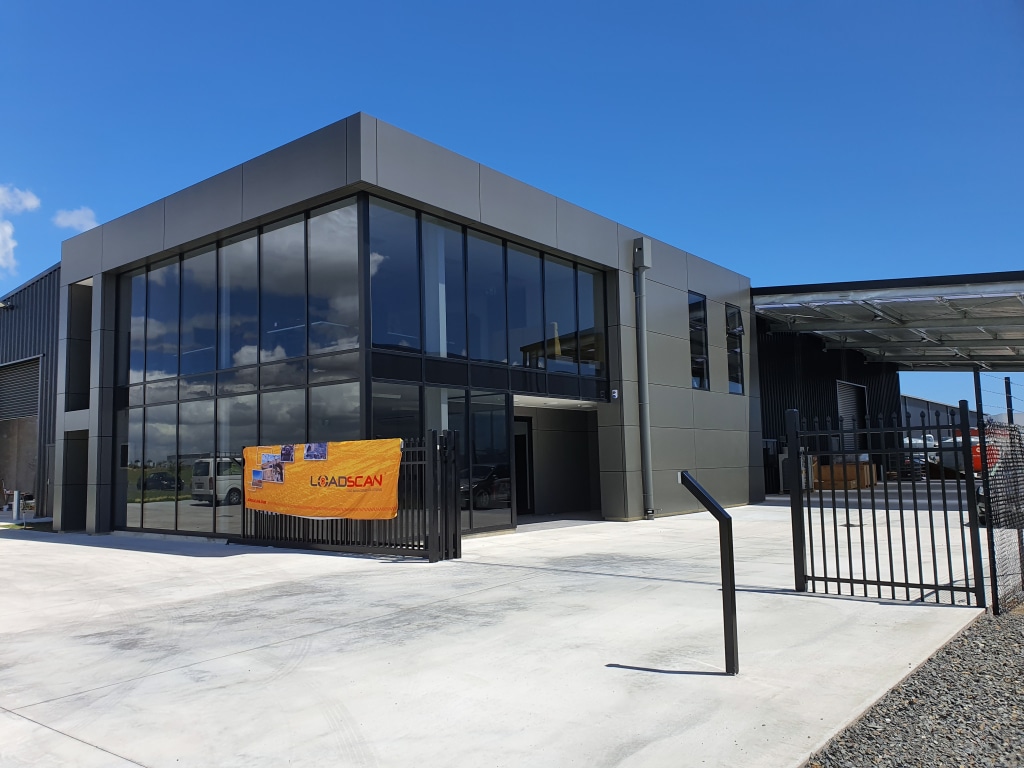