Optimizing Mining Operations with Pitram and Loadscan Integration at CSA Cobar The MAC [...]
Loadscan featured in Earthmoving Equipment magazine
Australia’s leading magazine for the earthmoving industry
VOLUME SCANNING TAKES A NEW FORMAT
For many major infrastructure projects on the horizon in Australia, the ability to tally the movements of materials onto, off and around site is a key logistical challenge. Loadscan is aiding civil construction sites for this process with its original load volume scanner (LVS) and its recently launched conveyor volume scanner (CVS).
Load volumes are traditionally computed from bulk densities (mass/volume ratios), but this method can be inaccurate. The LVS provides an exact picture (with plus or minus 1% accuracy) of the quantity of material being moved.
FULTON HOGAN TRACKS OVER A MILLION CUBIC METRES WITH LOADSCAN
Fulton Hogan currently use Loadscan’s LVS system for keeping track of more than a million cubic metres of material at a landfill rehabilitation process, which enables the company to gain a more precise understanding of the amount of materials being shipped on a daily basis.
Fulton Hogan previously used scales to weigh truckloads. Initially thinking they had 21 cubic metres on a truckload, using the LVS, Fulton Hogan soon discovered the number was closer to 17 cubic metres. This meant they saved paying for an extra four additional cubic metres of material.
Mr. Navarro, of Fulton Hogan, says the conventional method of measuring these vast quantities of materials is to use a system of weighbridges and to charge subcontractors based on the weight of the transported materials.
“There are issues with this method as it doesn’t account for increased weight due to water,” Mr. Navarro says.
With three mobile scanners on site, Fulton Hogan are able to gain a more precise understanding of the amount of materials being shipped. The trailer mounted mobile (LVS-3TMM) model is a fully self-contained unit that can be driven to a site and setup and be operational in as little as 45-minutes. Because of its mobility, Fulton Hogan will be able to tow the system by SUV or light commercial vehicle to a new site when the project is complete.
The LVS utilises laser scanning and RFID technologies, combined with software that creates 3D model images of trucks, to measure the exact volume of the material loaded in a truck or trailer bin. The load data is saved to the cloud and available in real time, letting staff immediately access that information and reduce travel time between sites for Fulton Hogan.
“As we are spread across three sites, having load information stored on the cloud is vital. The last thing we want to do is drive between the three units just to pick up the uploads,” Mr. Navarro says.
Mr. Navarro says he was impressed with the technology and has recommended the system to other parts of the business for future use.
From large excavation projects, through to smaller civil projects the need for a system that can accurately tally the movement of aggregate and spoil being moved on, off and around worksites is a huge benefit.
NEW CONVEYOR BELT SCANNER HITS THE MARKET
When Loadscan’s clients repeatedly requested for the company to build a conveyor belt scanner off the back of their successful load volume scanner (LVS) it was time to take action.
The global leaders in payload profiling systems launched the sought-after conveyor volume scanner (CVS) late last year.
The CVS is a high-tech, yet easy-to-use, tool that allows users to see how much material is moving across their conveyor belt. The CVS product release has been highly anticipated throughout the civil construction community. It will provide accurate non-contact volume measurement of quarried materials, allowing the user to optimise productivity and gain ultimate production control.
With the CVS, operators gain an understanding of their material flow on a conveyor belt, including what’s passing through the belt every minute or every hour, how much is required to fulfil the target in one shift, and whether target has been achieved.
The first CVS went to longstanding Loadscan customer, Colin Parker of Daltons. Parker bought an LVS over 18 years ago and jumped at the chance to purchase one of the first CVS units available.
“My favourite feature of the CVS is the propriety software. It’s great for reporting as it integrates into our own database. We looked at similar machines but discovered that you’d have to write your own programme.”
“We use the CVS to scan bulk material, that we make onsite, to ensure the volume we produce is correct.
“Then the LVS scans our trucks leaving site to ensure the volume we are supplying to our customers is exactly they’ve ordered. It’s a highly accurate, transparent system.”
The Loadscan belt scanner uses a specially designed scan-head, with single laser, to continuously scan the full width of a conveyor belt at high angular resolution to capture accurate volumetric measurement of the material flowing by. The above-belt lidar laser measurement system is ideal for optimising yield of stone, sand or gravel product streams, and for managing extraction rates and inventory stockpiles.
“We are really excited about this product. The concept of a belt scanner has been around for a while – customers have been asking for it – and now we can deliver a well-designed solution that’s easy to install and affordable, that has a software interface that is stacked with functionality, and that’s user-friendly,” Carey West, Owner and Director of Loadscan said.
The Loadscan belt scanner gives users a clear understanding of inventory production rates (or contract crushing quantities) in volume and tonnes. It is available to order now direct from Loadscan.
Find out more about the LVS system.
Find out more about the CVS system.
Read case studies from mines using Loadscan on the civil construction page.
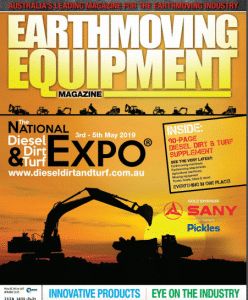
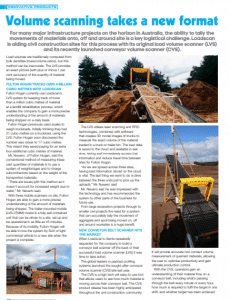
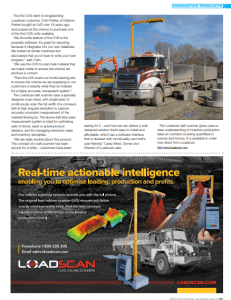