Optimizing Mining Operations with Pitram and Loadscan Integration at CSA Cobar The MAC [...]
Underloading could be costing you a fortune!
Underloading requires additional truck movements to shift the same amount of material, increasing costs and reducing profits.
Our expertise in mining and technology enables us to help mines maximize productivity by optimizing every load, thereby increasing trucking factors and improving profits.
Our load volume scanner accurately measures all loads and automatically generates 3D scan images that clearly indicate underloading, enabling corrective action (including operator training and coaching) to be taken.
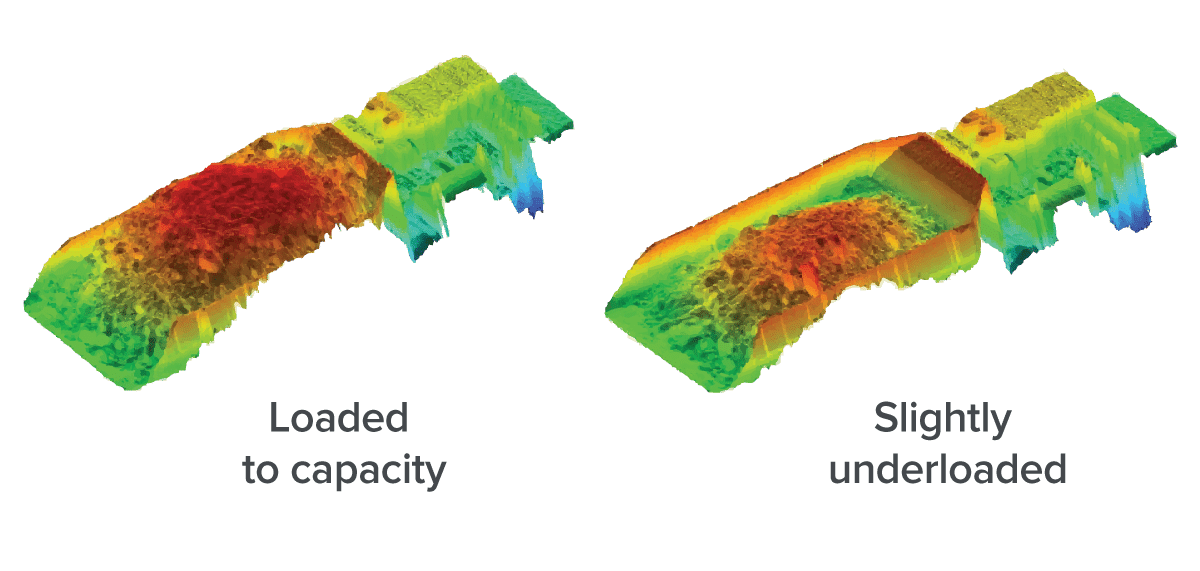
Loaded to capacity
40 tonne payload = 22.2m³
= 10,000 truck loads
Slightly underloaded
34.5 tonne payload = 19.2m³
= 11,594 truck loads
Underloading requires 1,594 additional truck loads
An example of Sandvik TH540 to shift 400,000 tonne material
(Based on density factor of 1.8)
Optimum loading has a significant influence on fuel consumption.
With big mining trucks, fuel is a major cost contributor. Analysis carried out by the University of Queensland into fuel consumption relative to load size shows some interesting facts.
Based on an analysis of CAT 793D trucks (250 tonne rated capacity), it was found that when underloaded, fuel consumption increased at a similar rate to when overloaded! It became evident that there is an optimal loading ‘sweet spot’ where fuel consumption (and resulting CO2 emissions) are optimized.
The Mine Payload Scanner (MPS) enables mines to identify sub-optimal loading in real time and to take immediate corrective action. The MPS is a key weapon in helping to reduce unnecessary fuel consumption and CO2 emissions.
University of Queensland, “Reducing Fuel Consumption of Haul Trucks in Surface Mines Using Artificial Intelligence Models”