Optimizing Mining Operations with Pitram and Loadscan Integration at CSA Cobar The MAC [...]

Enhancing efficiency at
P.R. Russell with Loadscan LVS
Project Details
CATEGORY: | Bark, Mulch & Compost |
LOCATION: | New Hampshire, USA |
WEBSITE: | prmulch.com |
PR Russell, a leading producer of bark, mulch, and compost products based in New Hampshire, has solidified its position as a dominant player in the bulk supply market in the region.
As one of the first companies in the USA to implement the Loadscan Load Volume Scanner (LVS), PR Russell has revolutionised its operations, significantly enhancing efficiency and accuracy in product measurement and loading processes.
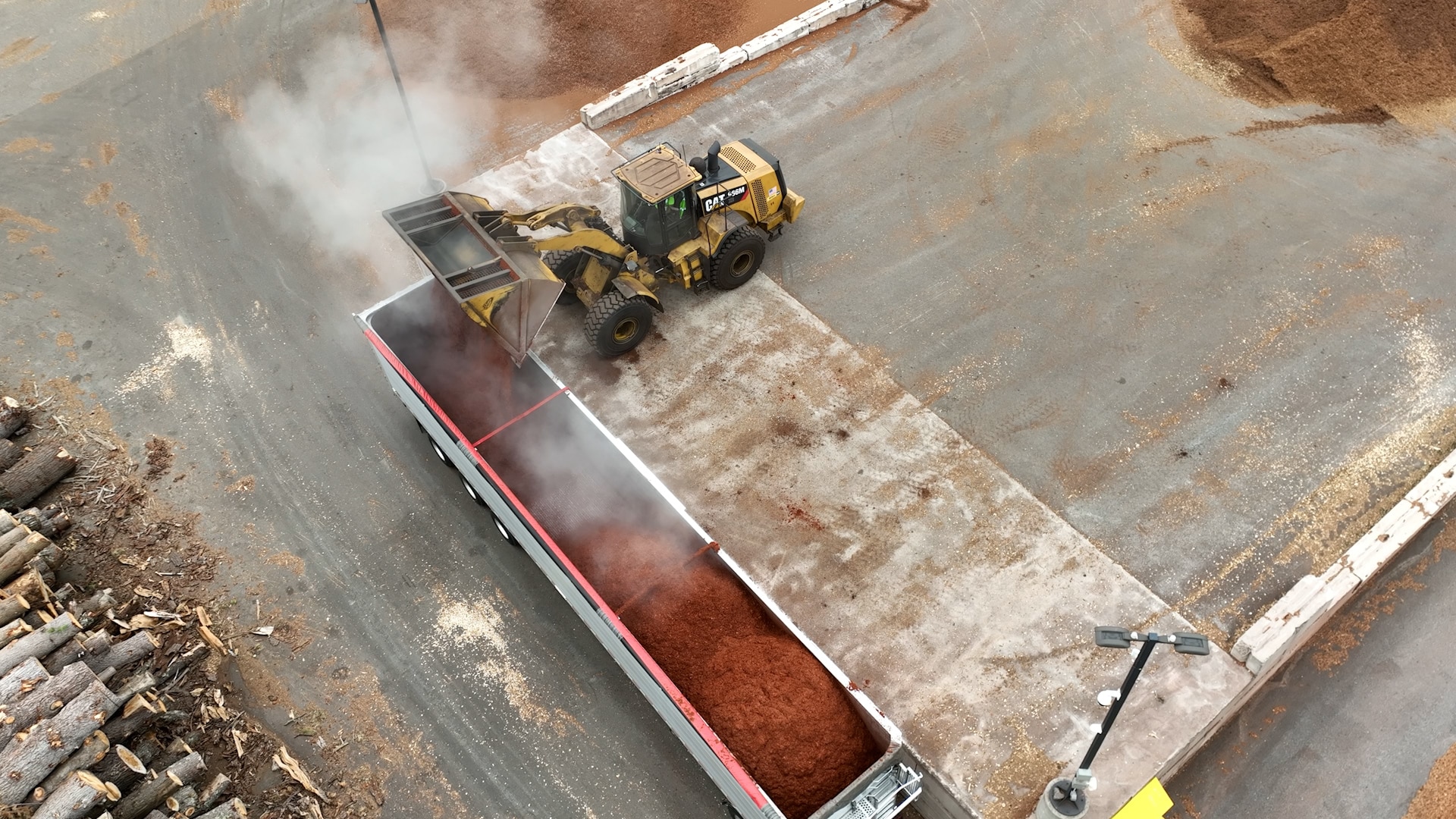
Background on PR Russell
Established with a commitment to quality and reliability, PR Russell has become a cornerstone of the bark and mulch industry in the USA’s North-East.
The company is known for its dedication to providing high-quality products while ensuring customer satisfaction. However, like many businesses in the bulk material industry, PR Russell faced challenges in measuring and loading products efficiently. Traditional methods often led to discrepancies, customer complaints, and wasted time.
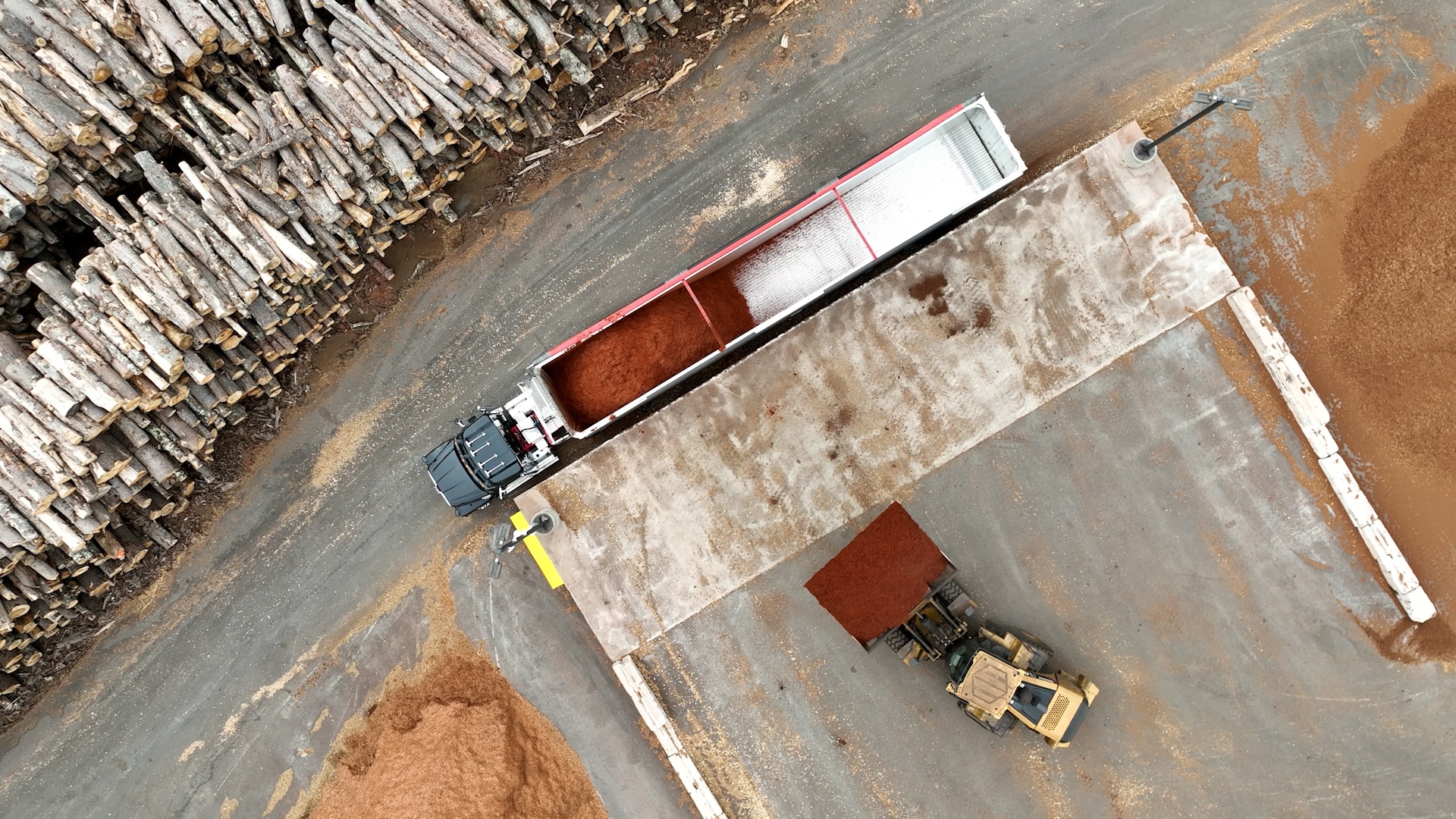
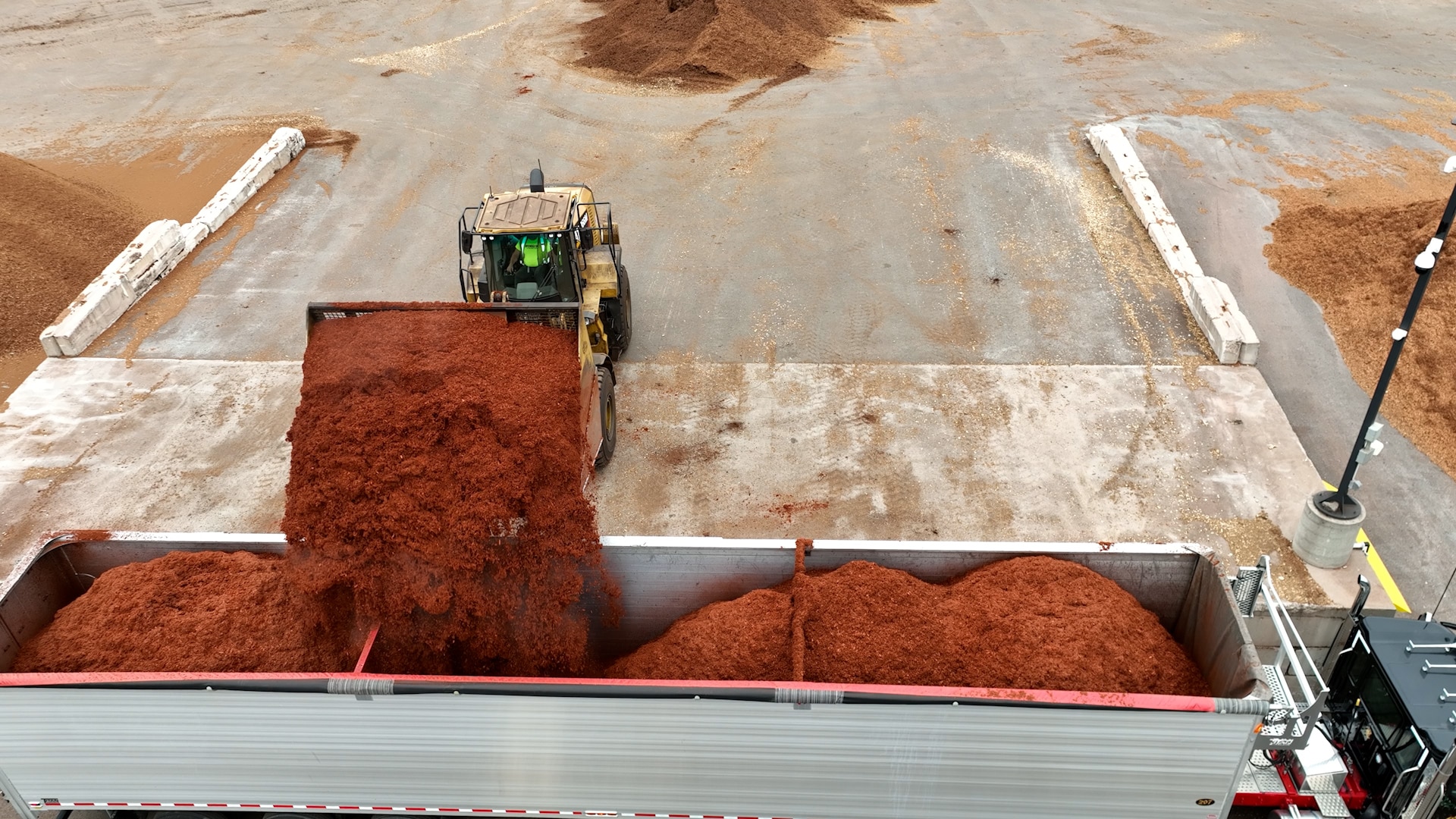
Challenges prior to Loadscan implementation
Before adopting the Loadscan LVS, PR Russell relied on manual measurements to determine the volume of material loaded onto trucks.
Marco explains the limitations of this approach: “We would physically measure the trailer and put lines in the trailer every ten-yard increments. So that was a guideline for the loader operator, but not efficient.”
This system was prone to human error, leading to inconsistencies in the loading process. Additionally, the company faced significant challenges with customer complaints regarding perceived short loads.
“There was a lot of complaining in the past of, ‘Well, we think this is three yards short,’” Carrier recalls. “There was always room for discrepancies.
“That’s how we did it in the past. And, like I said, not very efficient.”
This uncertainty created friction between the company and its customers, undermining trust and satisfaction.
The shift to Loadscan LVS
Recognising the need for improvement, PR Russell decided to invest in the Loadscan LVS, a transition Marco describes as a game-changer.
“Now loading is just loading. Come to the ramp, we’re going to load you up and you move on, so we saved a lot of time.”
The LVS technology makes the measurement process much more efficient, allowing for precise volume calculations without the need for manual intervention.
Efficiency gains
With the implementation of Loadscan, PR Russell experienced substantial time savings during the loading process. Carrier highlights that the need for the truck driver to monitor the loader operator has been eliminated.
“The loading was a process where now it’s just streamlined,” he explains.
This newfound efficiency has allowed the company to serve more customers in less time, ultimately leading to increased productivity.
In addition, the accuracy of the Loadscan system has transformed how PR Russell manages its operations.
“Every time we did testing, it was on the money,” Carrier states, pointing out that the consistency has virtually eliminated customer complaints about short loads.
“Once we had that system [Loadscan LVS], that went quiet. We don’t talk about that anymore.
“It’s a big deal…and it’s accurate,” he adds.
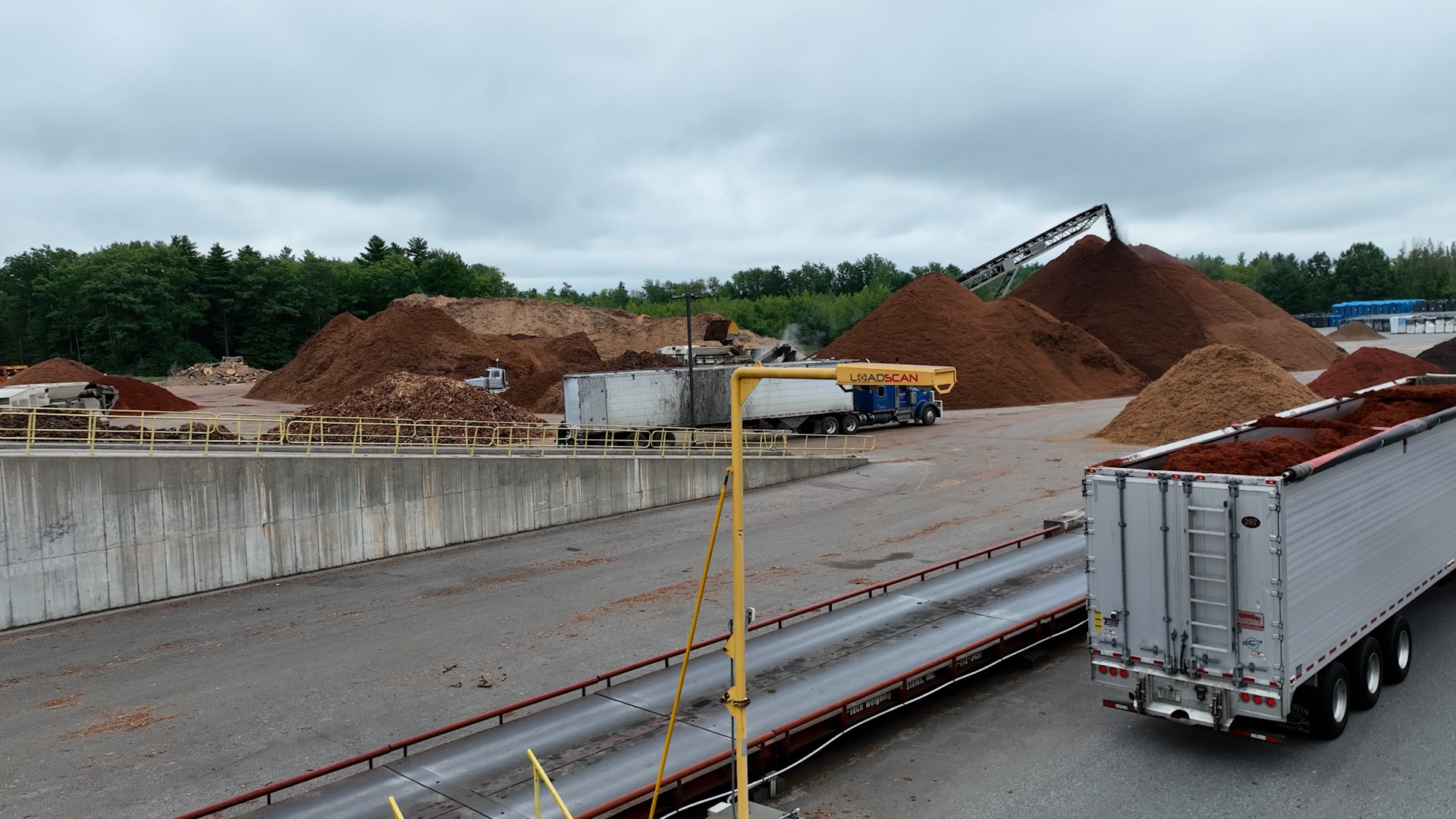
Improved measurement and training
The Loadscan LVS has not only enhanced operational efficiency but has also improved the way the loader operators operate.
Carrier emphasises the importance of measurement in the improvement process: “In order to improve it, you have to measure it. If you can’t measure it, you can’t improve it.”
“If you can’t measure it, you can’t improve it” – Marco Carrier, PR Russell
The Loadscan system provides precise data, allowing operators to understand their performance better.
“It was really a great deal for us. It saved a lot of time; it’s a good training tool for our loader operators.” Carrier explains.
This training aspect has been crucial, as operators can now receive immediate feedback on their performance. For instance, if a customer requests 80 yards of product but an operator mistakenly loads 81 yards, the system flags the discrepancy, enabling corrective action.
Navigating volume and weight challenges
The bark and mulch industry often deals with a wide range of different products, and Marco points out that the weight and volume of the materials handled at PR Russell can vary significantly.
“We deal with both extremes. When we deal with cedar bark, you can put 100, 110 yards onto a trailer and be at legal weight. If we deal with our aged material, once we get to 72 yards, we’re at weight capacity, so it’s a huge variation in that case.”
This presents challenges in accurately converting between weight-based purchases and volume-based sales.
Before using a Loadscan volume scanner, PR Russell struggled with this conversion.
“So this is where we would scratch our head a lot of time if we didn’t have a good way to measure the yardage.
“We did not really know how to do our conversion between everything we buy by weight to everything we’re selling by volume,” he says.
With the Loadscan system, however, they have developed a better understanding of their operations.
“There’s always variation obviously, but we have a way better understanding of where we’re going,” he asserts.
The bottom line: A valuable investment
Reflecting on the impact of the Loadscan LVS, Carrier declares,
“Looking back, it’s the best investment we’ve ever done for the industry.”
“…it’s the best investment we’ve ever done for the industry” – Marco Carrier, PR Russell
This statement underscores the profound changes the system has brought to PR Russell’s operations, highlighting the benefits of increased efficiency, improved accuracy, and enhanced operator performance.
Conclusion
PR Russell’s adoption of the Loadscan LVS has transformed its operational efficiency and customer satisfaction levels. By moving away from outdated measurement techniques, the company has streamlined its loading processes, reduced complaints, and fostered a culture of continuous improvement through precise measurement.
As Marco aptly summarises, the investment in Loadscan has not only optimised their operations but has also set a new standard in the bark and mulch industry, highlighting the significant advantages that technology can bring to traditional industries.